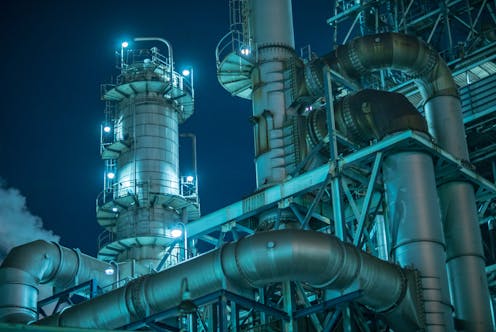
New Zealand burns the equivalent of 108 litres of petrol every second in coal and natural gas to generate heat for industrial processes. This burning of fossil fuels for industrial heat generates 28% of New Zealand’s energy-related emissions.
Industry needs vast quantities of heat for a wide range of activities, including to process staple foods, to manufacture materials for building homes, and to produce packaging for everyday goods.
But it’s very clear that to achieve a net-zero carbon economy by 2050, we need to ramp up the use of renewable energy technology to generate industrial heat, instead of burning fossil fuels.
The government is using a carrot-and-stick approach to drive the transition to low-carbon and renewable energy. The “stick” requires industry to phase out coal boilers for low and medium temperature heat applications by 2037. New natural gas exploration has also effectively ended, which will lead to future decreases in gas supply.
The “carrot” is the Government Investment in Decarbonisation Initiatives fund. The results so far are significant, with industry turning to tried and true solutions: energy efficiency gains, biomass boilers, electrode boilers and heat pumps, sometimes combined with electrical or thermal batteries.
These technologies are clean and green, but they are also scalable to industrial needs. Let’s have a look at what these different options are.
4 options for industry
The first option – increasing energy efficiency – is where all industrial businesses should start their decarbonisation journeys. It reduces the need to supply heat in the first place. Minimising heat demand also means replacement boilers can have smaller capacities, reducing investment costs.
The second option is to use biomass boilers. Over the past couple of years, biomass boilers have been rolled out to several large industrial sites.
These boilers burn biofuels, usually a byproduct of the wood processing sector such as sawdust, wood chips and wood pellets, to generate the required steam and hot water for a site. Fonterra, for example, is currently building a new 30-megawatt biomass boiler at its Waitoa site.
Biomass boilers provide a like-for-like replacement for fossil fuel boilers. But their use is not straightforward. No one really knows what the future availability of low-cost biomass will be due to the rapid expansion of the market in recent years, uncertainty around biomass sources and increase in demand.
The third option is to use electrode boilers. These are cheap to install but they use electricity as the energy source. The cost of this heat is typically three times more expensive than from fossil fuels. Industry is also often exposed to the electricity spot market where price varies dramatically both daily and seasonally, which presents both a risk and opportunity.
Dairy manufacturer and supplier Open Country Dairy, aided by “smart control” technology from Simply Energy, recently installed an electrode boiler alongside its existing coal boiler. The electrode boiler turns off when the electricity price is high, shifting load to coal, and turns back on when the price is sufficiently low. This is a cost-effective solution but invariably an interim measure as coal phases out.
The fourth option – heat pumps – uses a different type of technology. On paper, industrial heat pumps have the potential to achieve over two to three times the performance levels of biomass or electrode boilers, although often at lower heating temperatures. Better performance means proportionately lower operating costs. Current heat pump technology can service heating up to about 90°C.
Meat processing sites like ANZCO and Silver Fern Farms, both near Christchurch, are using heat pumps to recover and upgrade waste heat from their chillers to generate the hot water they need. This is another smart way of using conventional technology.
Baca juga: Climate explained: could biofuels replace all fossil fuels in New Zealand?
In the future, we need heat pumps to far exceed 90°C to increase their applicability to a wider range of industrial site. In Europe, many current technology demonstration units can now provide heating up to 150°C using an HFO refrigerant (synthetic fluorinated greenhouse gases) or CO₂.
HFO refrigerants were positioned as the answer to ozone-depleting gases but recent research expresses concerns about them degrading into “forever chemicals” with serious implications for human and environmental health. The European Union now plans to rapidly phase out and ban their use by 2026.
MAN Energy Solutions, which has recently partnered with Fonterra, offers a CO₂ heat pump that can also generate hot water at 150°C at a heat-to-electricity-use performance ratio of nearly three. This means it only uses one third of the electricity to generate the same amount of heat as an electrode boiler.
These four options all have critical roles to play in decarbonising New Zealand industry. Different sites will demand different solutions that will often combine multiple approaches to achieve the most cost-efficient solution.
Need for local solutions
Traditionally, New Zealand has been an energy technology importer. However, high demand for cutting-edge boiler and heat pump technology in much larger markets in Europe and elsewhere could make it difficult for New Zealand businesses to access necessary plant and technical support without long wait times.
If we could develop and manufacture our own, we could provide customised solutions for New Zealand industry. Many of the associated “green” manufacturing jobs would also be located here at home.
Baca juga: Time to tap in to an underused energy source: wasted heat
Decarbonising industrial heat presents a massive challenge but also an opportunity. The challenge is to make the energy transition quickly enough to limit climate change while keeping the energy costs sufficiently low to stay in business.
As we make this transition, we also need a paradigm shift in attitude and ambition towards research, development and manufacturing pathways for advanced technology to maximise the benefit to New Zealand Inc.

Timothy Gordon Walmsley receives funding from MBIE.
James K Carson receives funding from MBIE.
This article was originally published on The Conversation. Read the original article.