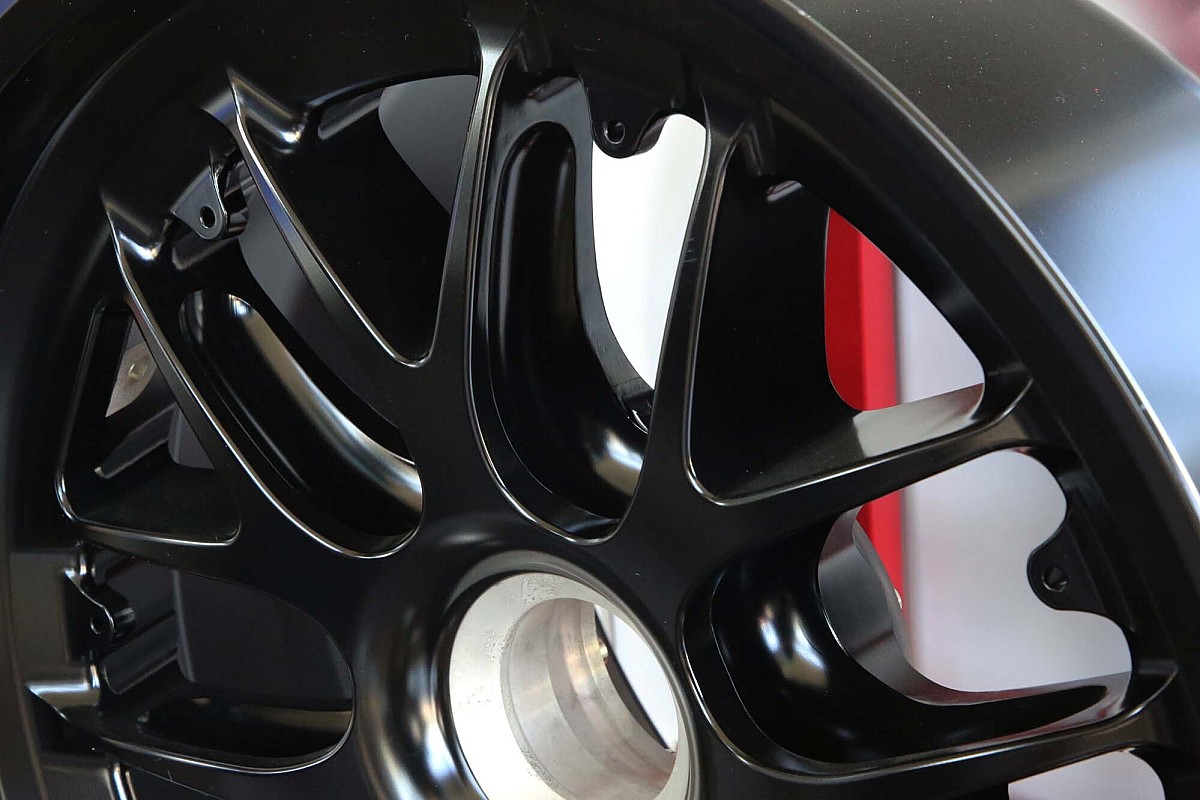
Even now, Japanese components big and small are contributing to the performance of F1 cars. And all the wheels used by F1 cars are produced in Japan.
From the start of the 2022 season, F1 wheels were increased in size from 13 inches to 18 inches. At the same time, it was decided there would be a single supplier, and BBS forged magnesium wheels were selected in the tender.
BBS first entered F1 in 1992, when it began supplying forged magnesium wheels to Ferrari. During the era in which Michael Schumacher dominated the sport at Ferrari, he had the support of BBS wheels.
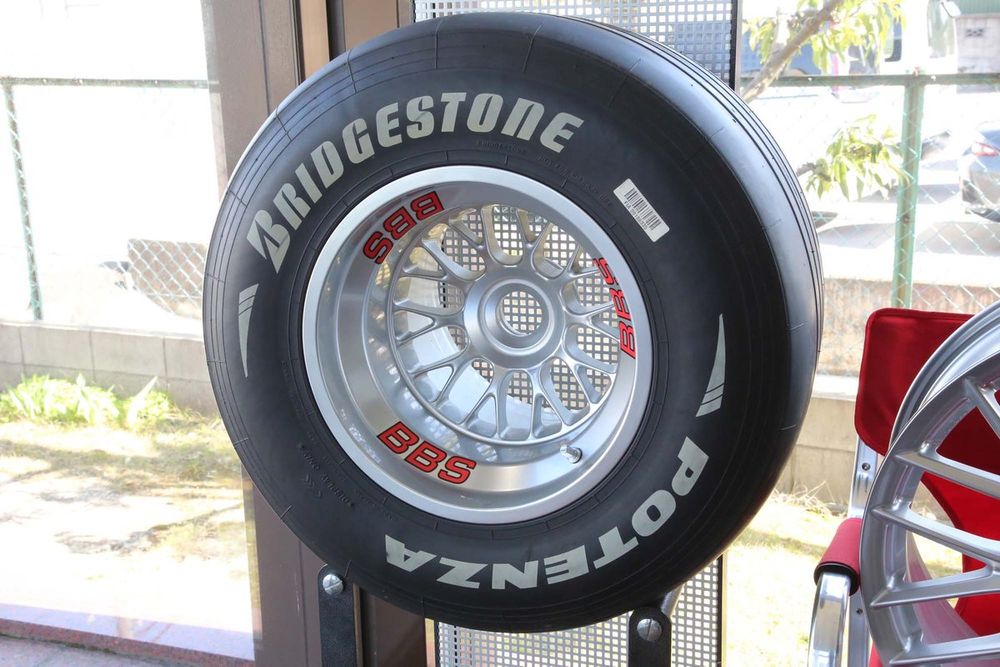
All of these BBS forged wheels are produced in Takaoka City, Toyama Prefecture. Indeed, you might be surprised to learn that they are forged on the same production line as wheels sold to the public. These forged wheels are then sent to Germany for final machining and to be painted, before being delivered to the F1 teams.
Roots in making swords – what exactly is forging?
When it comes to metal products, casting, the process of melting metal and pouring it into a mould, and machining, the process of cutting the raw material metal down to size, are common. Forging on the other hand is a process that may not be familiar to many.
In essence, forging is a process in which the metal is struck to create the desired shape. In fact, it’s a method that has been used since ancient times, and in Japan, it corresponds with the way craftsmen make swords.
Many of you will probably have seen images of swords being made by striking Tamahagane, a special type of steel, with a hammer. By striking the metal repeatedly, the space inside the metal is reduced, the metal fibres themselves become finer and more uniform, and the result is a strong and hard metal product.
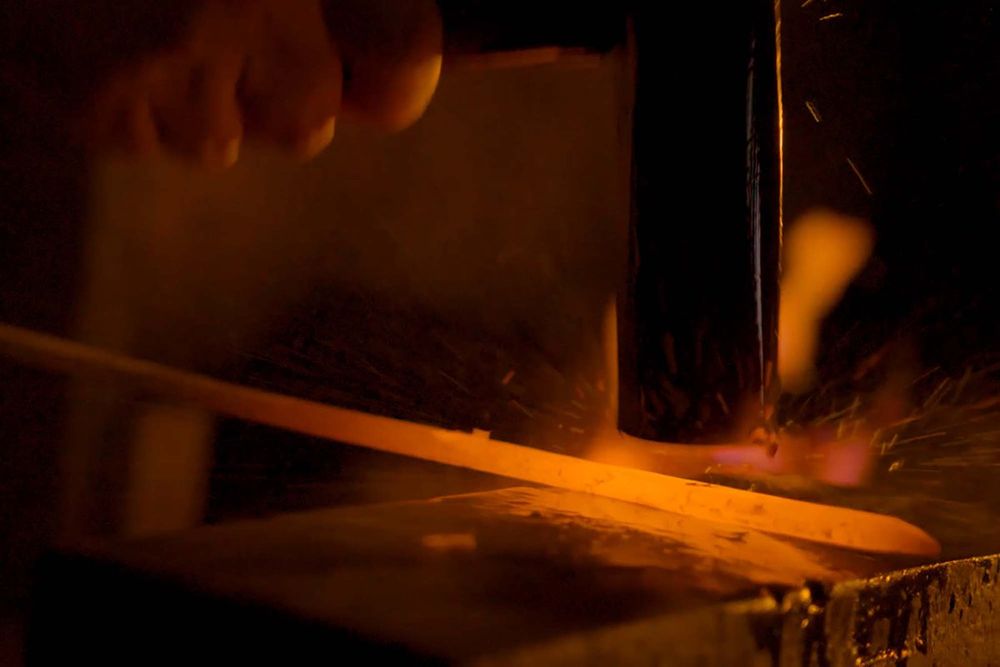
Not only on F1 cars, but the wheels on all cars are subject to large loads. When the power of a car is transmitted to the road, or when the uneven surface of a road has to be absorbed, wheels are indispensable. To withstand these loads, a high level of strength and rigidity is required, and forging is the ideal way to meet these requirements.
However, that’s not the only advantage of forging; a characteristic of ‘suppleness’ is also imparted during the process. By deforming flexibly, forged wheels can absorb loads and prevent breakages. They aren’t just strong.
BBS Japan’s head of technology Takashi Murakami explains the difference between casting and forging by comparing ‘onigiri’ and ‘omochi’, both products made from rice but with very different characteristics.
‘Onigiri’ are savoury rice balls with a flavoured centre, made using ordinary cooked rice, while ‘omochi’ is a traditional Japanese food made by steaming glutinous (‘sticky’) rice and pounding it repeatedly with a mallet.
He says: “‘Onigiri’ are just moulded, the rice itself keeps its shape and it can easily break into pieces and fall apart. On the other hand, with ‘Omochi’, the grains of rice themselves are crushed by a pestle so that they stick together. That means that they don’t fall apart like ‘onigiri’ and they can be pulled and extended [like dough]. If you think of it that way, the difference between casting and forging becomes easy to understand.
“By using forging, you can aim for lightness without sacrificing strength. Also, stiffness can be added as an extra bonus. Then it’s a question of striking the correct balance between increasing stiffness or taking advantage of the suppleness that is a benefit of forging.”
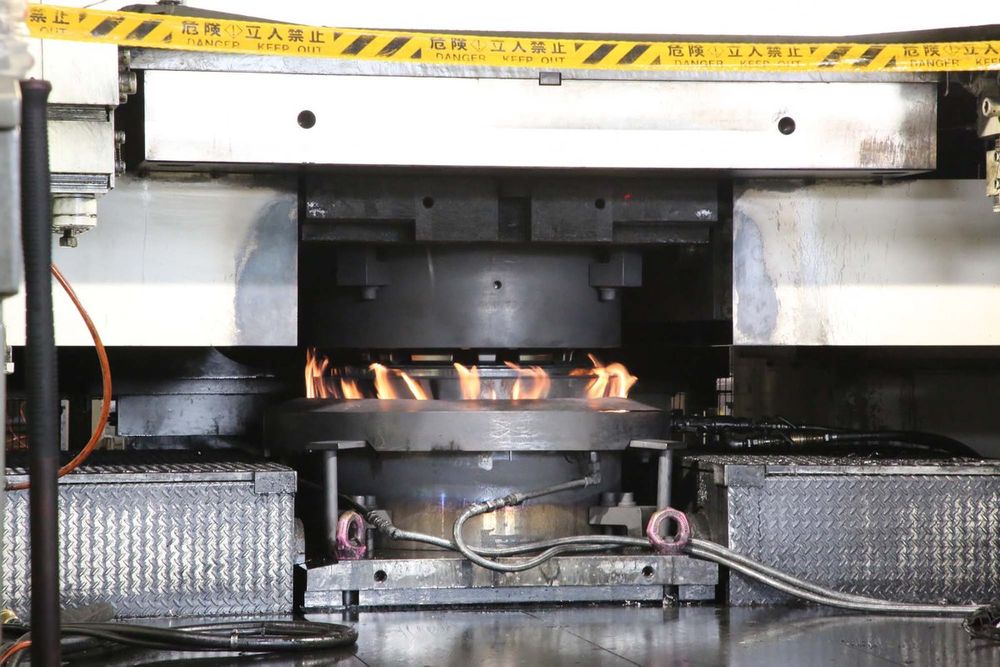
The BBS factory is packed with a huge number of pressing machines. These allow for a load of up to 12,000 tons to be applied to ‘billets’, which are cylinder-shaped lump of metals. These billets are struck many times over and eventually take the shape of a wheel.
The role of the hammer in ancient times is now played by these gigantic pressing machines. This way, the billet is transformed into something much stronger and more flexible, which forms the basis of an ultra-high performance wheel.
Why make wheels in Takaoka City?
Metalworking is a major industry in Takaoka City, Toyama Prefecture, where BBS is headquartered. Starting with copperware around 400 years ago, when a caster was invited by Toshinaga Maeda, the feudal lord of Kaga Domain (roughly equivalent to modern-day Toyama and Kanazawa Prefectures), various metal products have been produced.
Even now, around 90 percent of Japanese copperware is made in Takaoka City. In addition, even before that, during the Nanboku-cho period (1336-1392), a group of swordsmiths known as the ‘Uta school’ established themselves in Etchu province (in modern-day Toyama Prefecture), and continued producing swords in the area until the Edo period (1603-1867).
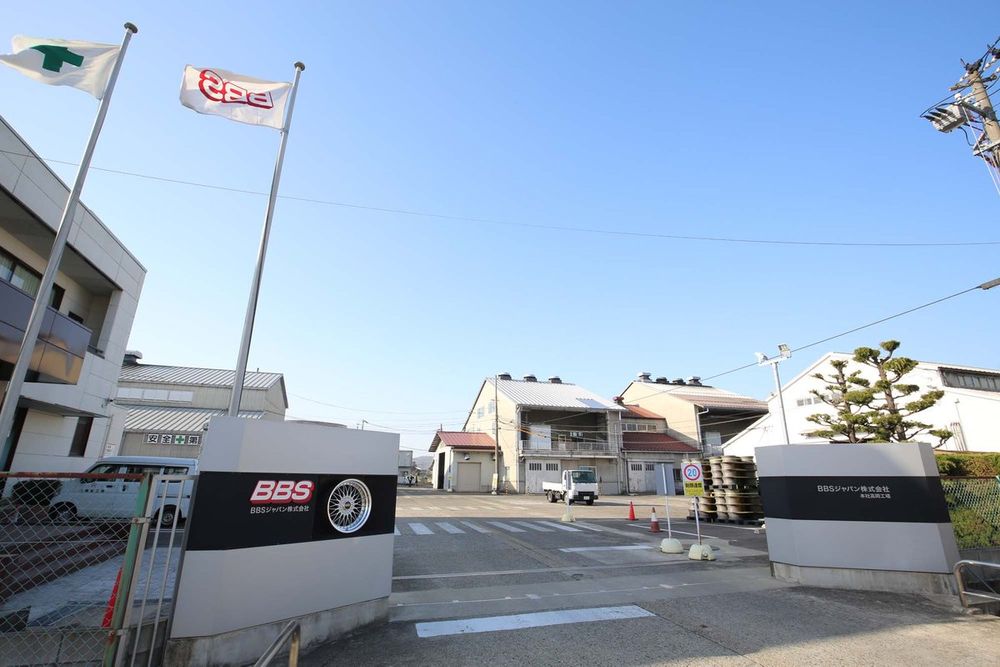
There is also the Tateyama mountain range in Toyama Prefecture. Here, there are abundant water resources and steep slopes, making it ideal for generating hydroelectric power. There are many makers of aluminium products and other materials that are using this natural source of energy within Toyama Prefecture.
From both a historic and geographic perspective, metalworking industries took root in Toyama Prefecture and Takaoka City. You could say it’s almost natural that wheels for the world’s highest-level racing series are made in such a place.
Mr. Murakami also says that the temperament of the people of Takaoka City is ideally suited to detailed metalworking and the creation of ultra-high performance wheels.
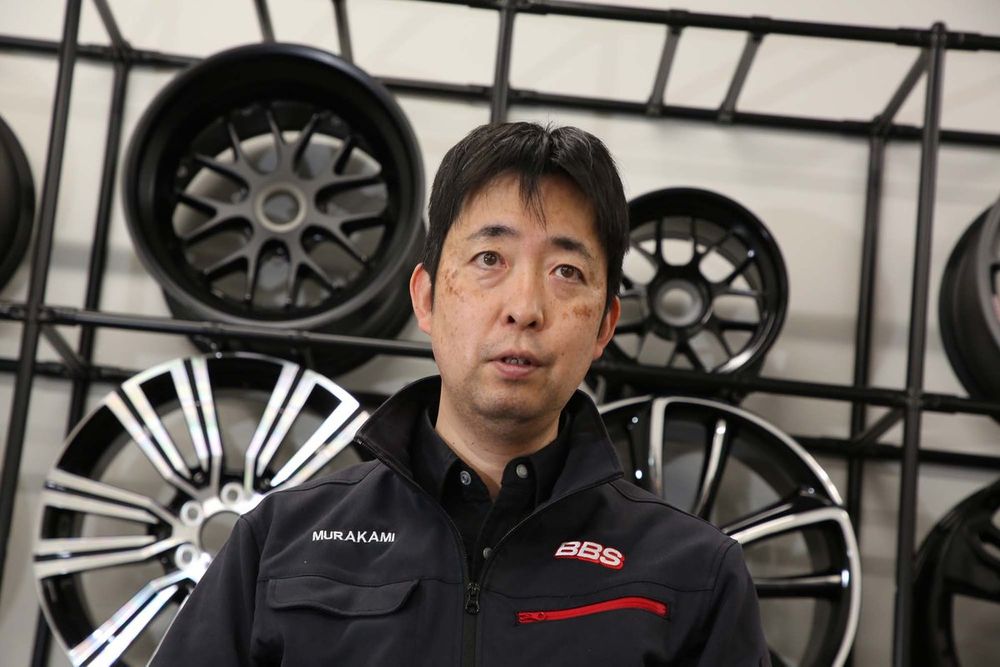
“I think the character of people from the Hokuriku region [on the northern side of the central part of Honshu, Japan’s largest island] is suited to this kind of craftsmanship. The people of this area are serious. They have a strong artisanal attitude and diligently get things done.”
Mr. Murakami himself is a native of Takaoka City, and underlines his belief that Hokuriku is the best region in Japan for making things.
“I have my roots in Hokuriku, and I think it’s an area with an environment that allows people to take their time to do things properly. Traditional crafts still exist here as a matter of course, so I’m glad that I can work here.
“You have the sea and the mountains nearby, as well as the city. Everything is at a good distance. It’s a place where you can have a good work-life balance.”
Aiming for the ultimate wheel
Producing wheels for F1, the peak of worldwide motorsport, as BBS does, may seem like the ultimate activity for a wheel company to be engaged in. But Mr. Murakami says there is still plenty more to do. This is the ‘beauty’ that BBS is obsessed about.
“As BBS, we are obsessed by beauty. The ultimate thing for me is to aim for the same level of perfection as Japanese swords,” explains Mr. Murakami.

“I want to make a wheel that pursues ‘functional beauty’ to the limit. A wheel that has high performance but can also back that performance up with beauty… if we can do this, maybe I will have nothing left to do.
“With each generation, we have been able to do things as suits the occasion, but there is still much left to do. We were able to make a wheel from ‘extra-super Duralumin’, and with the FI-R make a wheel with a different shape to the one we’ve used until now. Maybe that’s one answer, but I feel like there are other things we can do.
“What is the same level as a Japanese sword… even now, I can’t answer that. With Japanese swords, nothing is wasted, and each one has individual meaning. Seeing as we are obsessed with forging, I want to aim for something like that. If we can do that, I feel like we will be able to advance one step higher than those around us.
“I think aiming for the ultimate will be an eternal theme for us at BBS. If I can ask myself that question and find something to do with it in the future, I think I will be able to say that my life has been a good one, both as an engineer and as a member of society.”
For more info, click here.