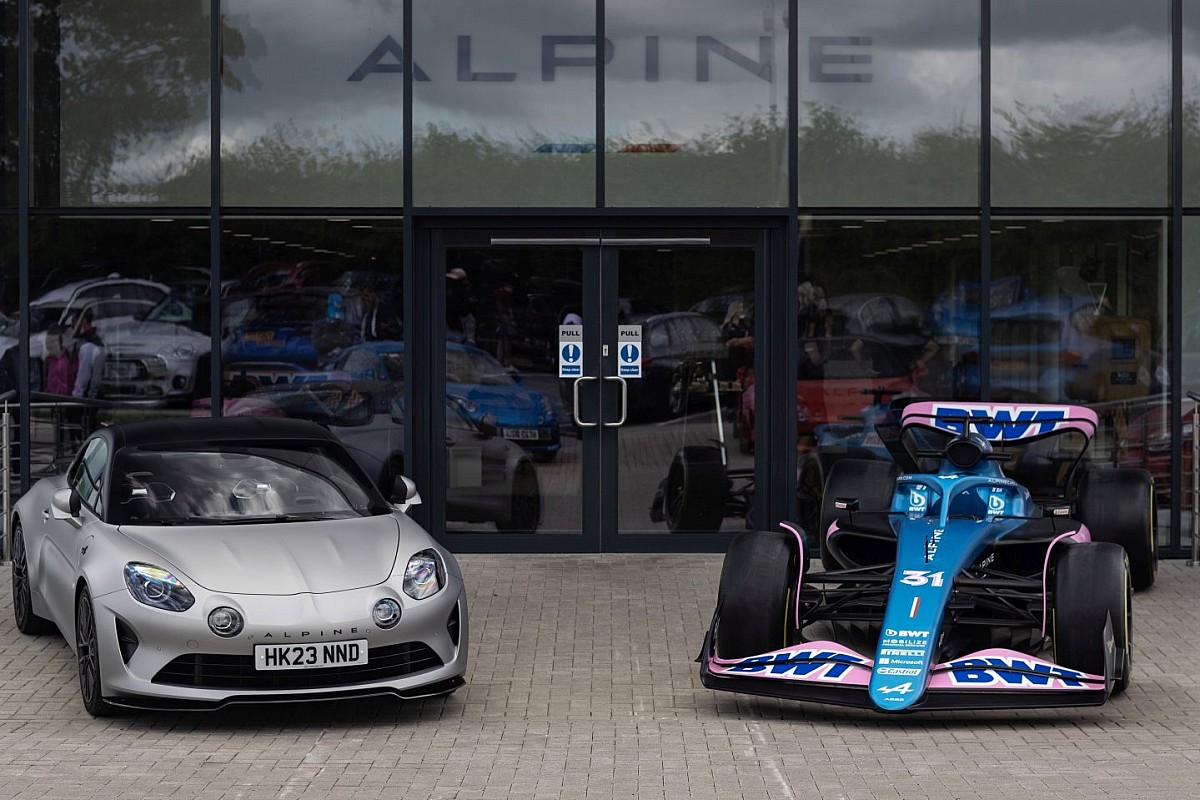
It’s a challenge that many teams have either faced in recent years or are currently tackling head-on.
At one extreme there’s Aston Martin, whose Silverstone factory – created for the birth of the original Jordan outfit in 1991 – had long ago outlived its useful life.
Owner Lawrence Stroll had the funding and commitment required to buy an adjacent site, build a completely new facility, and then demolish the old one to create more space for the next stage of the project.
PLUS: The Verstappen inspiration behind one of F1 2023’s other success
When finished there’s little doubt that the Aston base will be the best of any current team, simply because it was created from scratch to 2020's specifications with no compromises.
Others have opted to continue to develop, enlarge and generally upgrade facilities that have their roots in another era.
From a humble start with the ex-Stewart/Jaguar facility, Red Bull has created a campus by acquiring neighbouring buildings and erecting new ones, notably for its growing Powertrains division.
Mercedes meanwhile has made huge changes to the site originally created as the home of BAR for the 1999 season.

It’s not an easy task. Apart from the obvious aspect of space, there’s the challenge of doing everything within a cost cap environment, while complying with planning and building regulations that cover aspects such as sustainability and environmental issues.
Then there are considerations such as the well-being of the staff – the goalposts have moved over the decades, and teams now have to create an optimum working environment or risk losing people to local rivals who can offer more.
Like RBR and Mercedes, Alpine is doing what it can with an existing facility - in this case, one that started as Benetton’s home in the early nineties.
"What you see is already a fairly compelling indicator of the commitment of the owners to getting the team into good fighting shape" Rob White
The man charged with running the Enstone site and keeping it up to date is operations director Rob White. He is best known as being the former head of the engine division in Viry, and as such, he was heavily involved in the championship-winning V10 and V8 engines and the early V6 hybrids, until a reshuffle a couple of years ago saw him move into a very different role at the UK base.
“Before we came, the site had been a quarry,” says White of Enstone. “It was used for light industrial uses, making pre-cast concrete buildings and bunkers and garages, the sorts of things that used to be around in the 60s and 70s. That was all gone by the time Benetton acquired the site when it was derelict.”
Through the Benetton and Renault eras – which saw four World Championship titles shared between Michael Schumacher and Fernando Alonso – the site grew in a piecemeal fashion as the team tried to keep up with rivals. Investment stalled in the Lotus/Genii era, but new impetus came when Renault bought back the team.
“We've got something that was re-acquired by Renault in 2016, and which has been heavily invested in in the very recent past,” says White. “And what you see is already a fairly compelling indicator of the commitment of the owners to getting the team into good fighting shape.
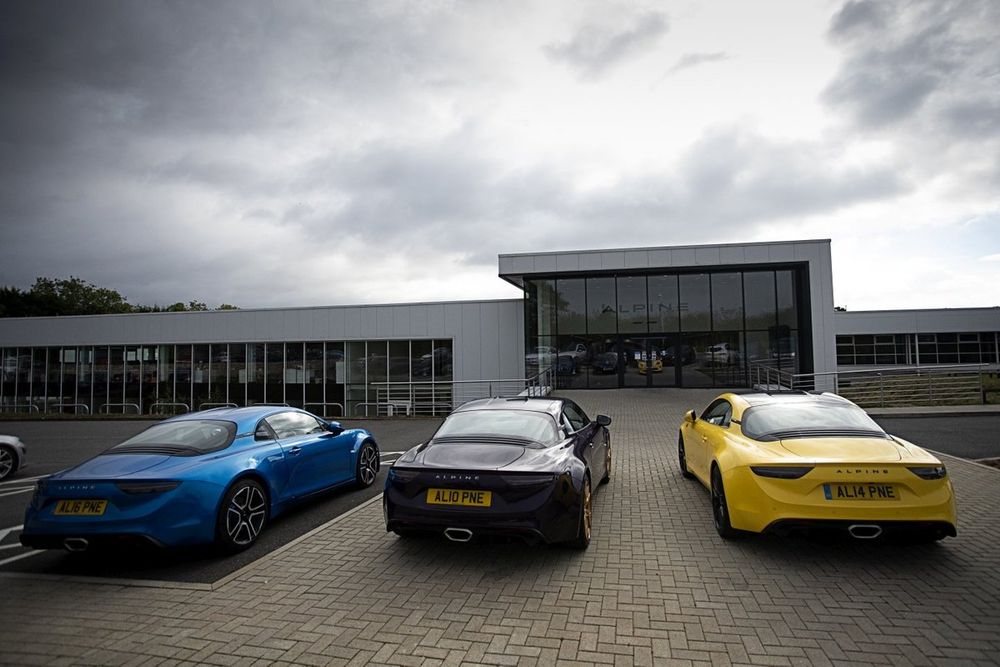
“It's difficult really to succinctly put into words, but it was a long, long way from where it needed to be. Where it is now, we're much better than we were, but clearly looking forward, we need to be stronger, we need to be bigger. And we've got specific equipment and infrastructure ambitions.”
Enstone may be surrounded by fields, rather than hemmed in like some other team bases, but that doesn’t make it any easier to expand.
“The privilege that we have to be located in this fabulous place in the middle of the Oxfordshire countryside means that we have to be responsible,” says White. “Which thankfully, comes relatively naturally.
“We have a duty to improve and curate the site, and we treat all of the impacts of our activity here very seriously.
“We've enhanced the site at every stage in recent times, and going forward, it will be more so. We've had to do things with it that if we hadn't needed or wanted to do them for our own business reasons, we'd have been compelled to do them for regulation and legislation type reasons, to do with carbon reduction.
"We are constrained because of the type of environment. Every time we touch the site, we need to make an ecological improvement, we're not able to degrade anything.
“We treat that very seriously, and have done so naturally for years, and long before these became hard requirements of the building regulations. But it does mean we have good support from our immediate neighbours.”
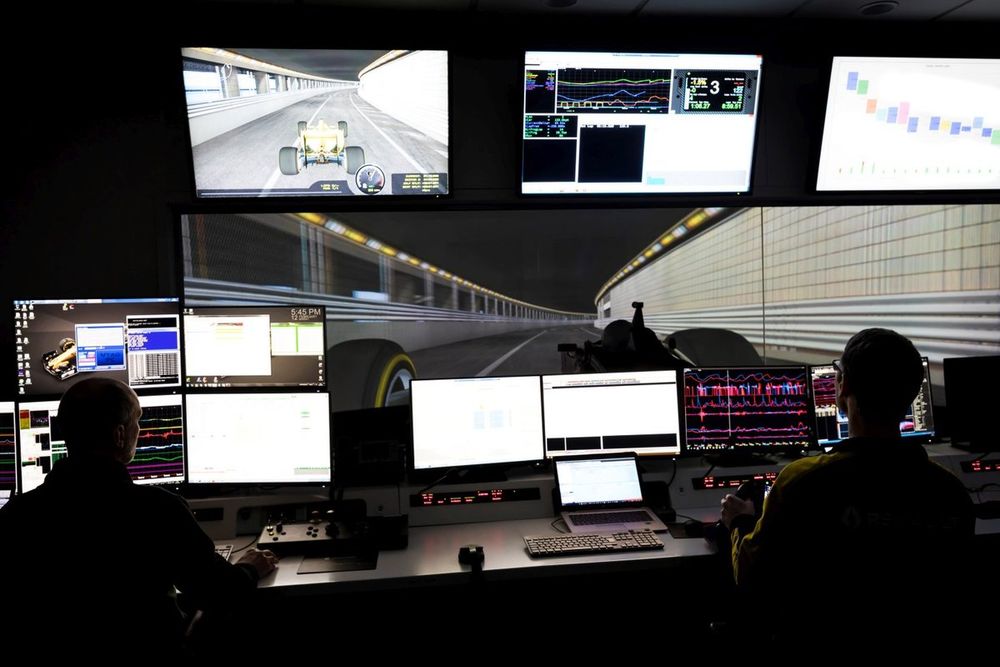
It also entails working closely with the local authorities: “We have a very transparent relationship with all of these people with a view to helping to tell a very good news story for the local area,” says White.
“We're by far the biggest local employer, and we're a prestige brand in the heart of a very beautiful part of England. It's definitely a responsibility to juggle those plates.
"Everything outside of the building also needs to be making a positive contribution. We've worked very closely to come up with an ecology plan that works. We've got some very precious and interesting plants and animals on the site. We've curated and improved those things, and not harmed them, at every single stage."
“We've got to deal with the challenges of operating on planet Earth in 2023" Rob White
F1’s carbon footprint has become a major issue for the sport as a whole, and all teams have been actively making their bases greener.
In Alpine’s case, a recent expansion of the ageing main building helped to create an opportunity to take a big step forward.
"There's 1000 square metres of new office space,” says White. “We had to make the building sound, as it is over 30 years old. And we had to bring it up to more modern standards.
“We've fixed the roof; it no longer leaks when it rains! But also we've massively improved the insulation, which is good for our energy consumption, and for our carbon footprint.
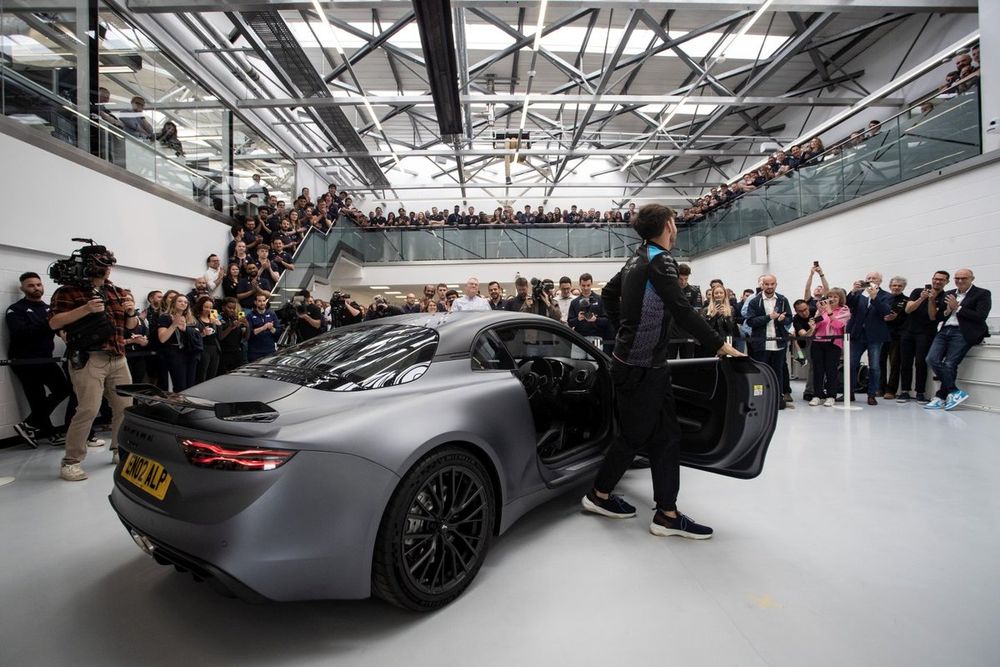
“We've electrified the space heating on the whole site using high-efficiency heat pumps, so there's no gas or old-fashioned direct electric heating. We've developed strategies along the way that I sincerely believe help us with making it a good place to work.”
On top of these changes, climate change has had an even more direct impact on Enstone operations.
“We've got to deal with the challenges of operating on planet Earth in 2023,” says White. “It rains a lot more frequently these days as a result of the global warming that we're all familiar with. When it rained a lot, as I said, it used to leak into the building, and it used to flood a chunk of the machine shop. It doesn't do that anymore.
“It's not quite as sexy as a new simulator, but we've got massively better storm drains than we had. And we've got to build better storm drains again. Again, these are to some extent regulatory requirements.
“But typically, we're ahead of the minimum regulatory requirement because we're more optimised, or we're more focused on the performance and efficiency of our installations. I just won't tolerate the machine that's supposed to be making patterns for the next floor upgrade being stopped because it rained, and the drains have overflowed.”
Such considerations aside the team is making the best use of its existing site by finding space for new infrastructure.
“We've generated another 700-plus square metres of floor space by the addition of a third storey on an existing two-storey building,” says White. “We've effectively put a new third storey on stilts above it.
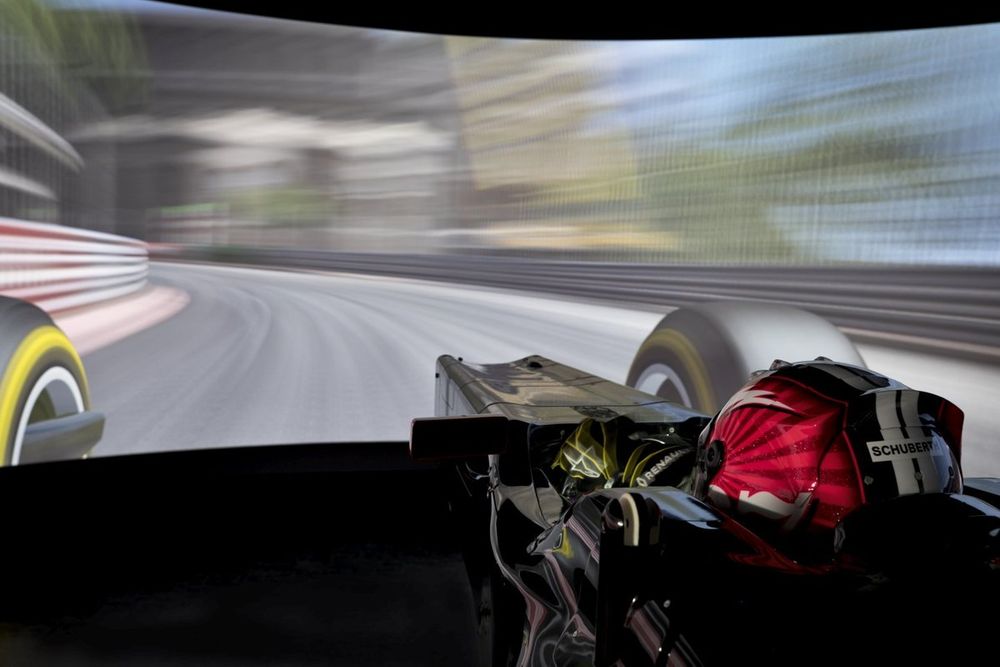
“This is a new composite production facility. We do have a recent state-of-the-art cleanroom for composites, but the upstream part of the composite production process was still in the bowels of the factory much as it would have been 20 years ago, and it's moved into a new location in the new building.
“If we look immediately beyond the completion of that composites building, our next project is to build a new facility which will house a state-of-the-art simulator. So that is committed, there's a planning application in for the building. The bad news is we’ve had to demolish the gym.
“We learned some things during COVID that we applied; we were well ahead of the curve in terms of how to operate buildings safely" Rob White
"The good news is that [the] secondary purpose of the sim building is to house the Human High Performance Centre, the new gym, which will be a massively good amenity for the Academy and Rac(H)er driver development groups, but also an amenity for the staff.
"It will be a net zero building, it will have solar PV [photovoltaic] on all of the available surfaces, as does the new composite production building.
“I don't want to over-egg that, because it's just part of what we do. When we built the existing simulator building, which opened a long time ago, it already had a small-scale PV installation. That's now closer to the end of its life than it is to the beginning. But this new extension will be properly net zero.”
It’s not just about the fundamental structures, but how they are used. The aforementioned extra office space helped to create a huge open-plan area for the designers and engineers.
All teams have been going in that direction over the years – a similar area is at the heart of the Aston development – but Enstone had lagged behind until recently. The latest step of integration was completed over this month’s summer shutdown.
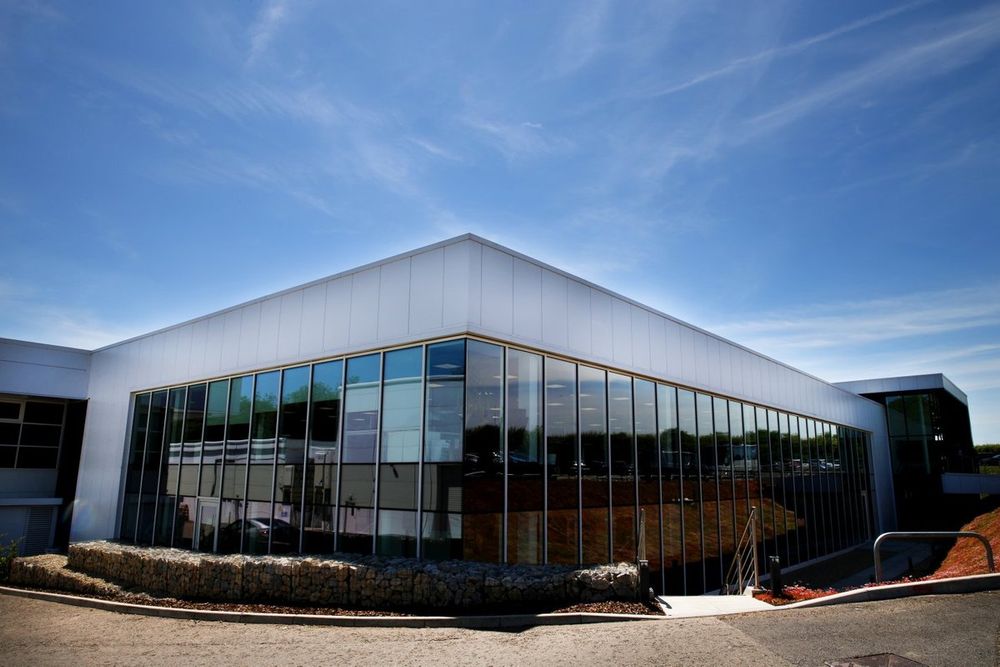
“It was a big undertaking to build this amazing, open plan, collaborative working space while continuing to design, develop, and operate the race car,” says White, “We weren't able to shut the site down, we weren't able to build it in a field next door and move in when it was ready. So we had to move people out into temporary locations.
“We turned up the working from home dial for a little while, we did a very aggressive timing plan. But it's not just creating light and space and desks, it's also about managing the environment in which people work.
“We learned some things during COVID that we applied; we were well ahead of the curve in terms of how to operate buildings safely during COVID. And some of those lessons have transferred into our plans going forward.”
Open plan working, with 280 staff members in the same room, helps to streamline communications.
“We paid a lot of attention to the asks of the people that would be working there,” says White. “It’s like some of the challenges when designing the race car, you've got a multi-dimensional optimisation to do.
“And it's very challenging to get the performance of the team right at the top of the list and make sure that all of the decisions that you take are oriented towards getting the most out of the people and delivering the most performance to the track.
“Some of the contractors or suppliers that we end up interacting with are not accustomed to being challenged on the product and service that they deliver by an individual or group of people that are so performance focused.
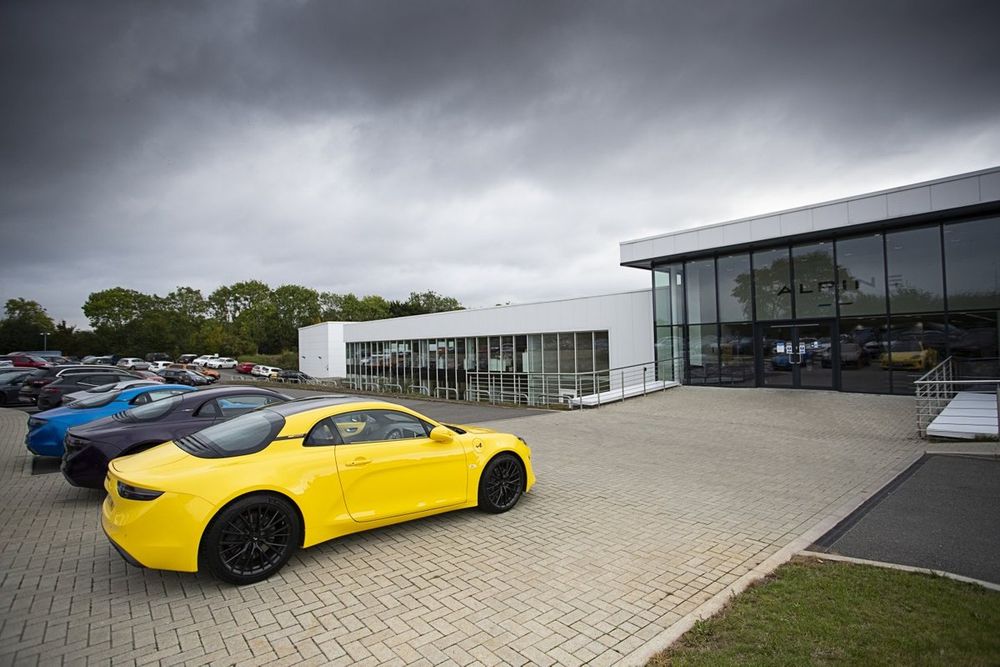
“And I like to think that we get good value, we get good performance out of them as a result of applying a little bit of F1 logic to things other than just the design of the race car.”
Decluttering the workspace has been a key element of the redesign: “Everything that the high-end engineering users would use, CAD stations, CFD, all of the processing power is now held centrally in data centres, accessed remotely from the desks.
"Fundamentally, we've done the classic stuff, we've de-partitioned, we've opened it all up, and we've brought daylight in to disrupt siesta time!
"For this team to be sustainable into the future, we need to look after our people, and we need to build a group of people who look after one another" Rob White
“The way in which we work is very agile, you can generate cross-functional teams very, very quickly, and we can have people co-located with their most significant collaborations very, very easily.
“And if you're a designer, a stress engineer or a CFD specialist you can park your laptop on any one of the desks and you can reach the equipment and software that you need to do your special subject.
“And your colleague next to you can be either a clone of yourself or he can be a colleague that you're interacting with on a project.”
A more efficient desk arrangement may sound a little esoteric, but this is a sport of marginal gains, and no stone can be left unturned.
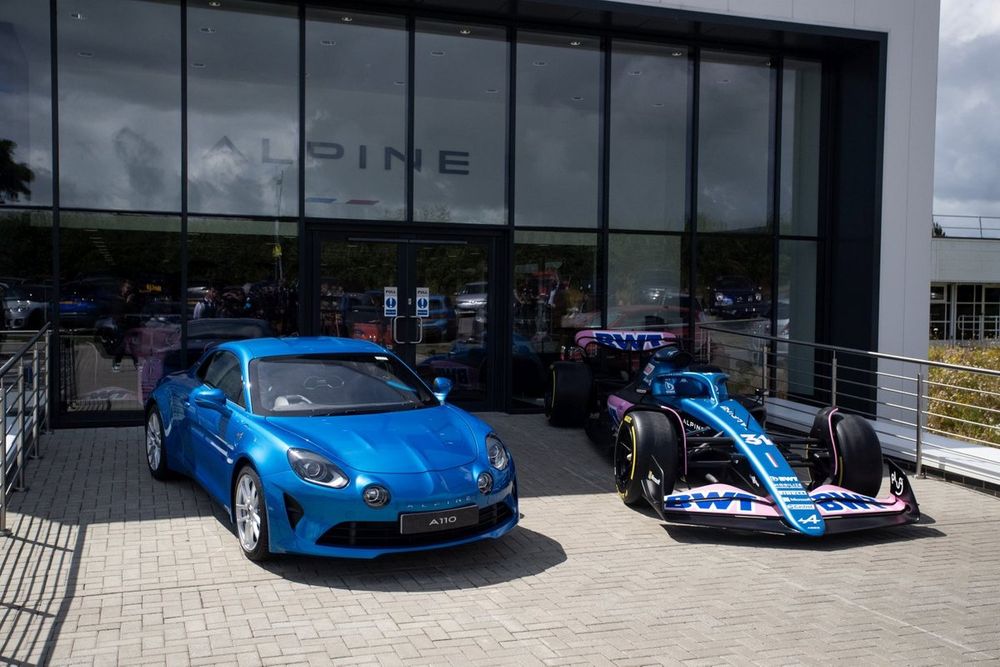
"Every design, development, infrastructure change, everything that we do is driven by lap time, extracting performance or improvements in race outcomes that are converted into points,” says White.
“We all understand that we've got to be super focused, we've got to be driven to eliminating the obstacles that stop us generating performance, and to generate performance faster, to detect performance with finer resolution, so we make better decisions and make more decisions more quickly, such that we can get the performance to the car."
As such getting the Enstone site working as effectively as possible, while making it an environment in which the best people want to work, is one of the keys to Renault’s ambitions for Alpine.
"The team at all its levels is absolutely committed to getting back to where we want to be,” says White. “This is a serious programme. Crucially, in my opinion, none of us that have won races or championships in previous years operated at that time at the level that we now need to operate at in order to win the next race, or the next championship.
“The game moves at such a pace, the bar is so high, and there are no silver bullets. And it's the classic people, tools, processes, and it's a very, very linear system, it all kind of adds together.
“This is a thing that requires determination, resolve, ambition, and performance at the right level in every discipline.
“And for this business, for this team to be sustainable into the future, we need to look after our people, and we need to build a group of people who look after one another. We're channelling values that that we absolutely believe will get us to the correct level in F1."
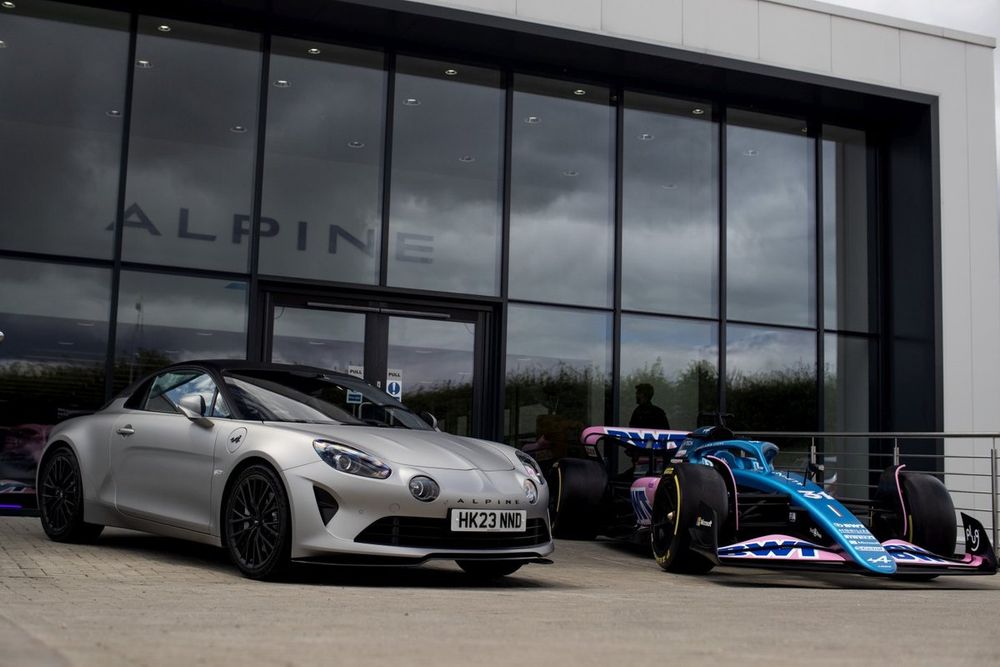