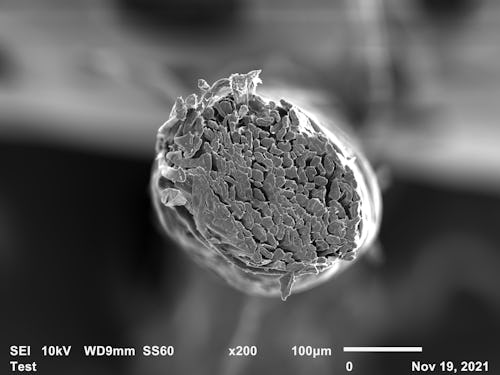
Against your skin, cotton feels smooth and soft — but on the microscopic level, it is a scraggly mess. Viewed at 100x magnification, a cotton thread looks like bundles of straw or clumps of hair. This quirk of nature is what led Dr. Luke Haverhals, the founder of Natural Fiber Welding, to ask a question few scientists had pondered before: what if you could take natural materials such as cotton and make them look and act like the technical fabrics we’ve grown accustomed to, down to the molecular level?
Haverhals’ answer is technology he calls Clarus, which turns cotton, hemp, wool, or any other natural fiber into sustainable, biodegradable super-threads that perform as well, or even better, than the synthetic competition.
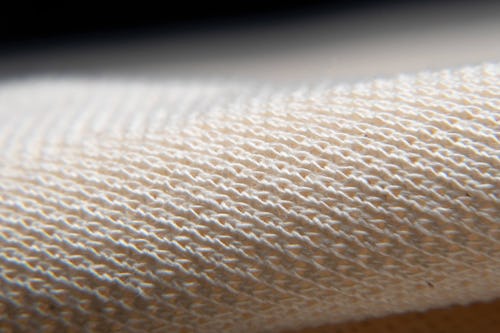
In 2021, the sports apparel sector generated $193 billion in revenue. Our sweat-wicking T-shirts, stretchy yoga pants, and heat-trapping base layers are almost entirely made of synthetic performance fibers such as nylon, polyester, and spandex. These fibers are so good at what they do because they’re made of identical chains of polymers and extruded in precise lengths specified by manufacturers.
The shape or structure of a yarn gives it its properties. Silk is shiny because of its triangular cross-sections. Wool’s warmth comes from its microscopic scales. Under a microscope, a polyester thread looks like a fiber-optic cable — every filament bonded to itself in a neat geometry that gives the material its useful properties: strength, durability, abrasion resistance, and moisture control.
“Nature reformatted.”
The problem is that the synthetic fibers that we’ve come to love are made of plastic, a derivative of fossil fuels. Fibers from these clothes come out in the wash and pollute our waterways, making their way out into the environment and even in our bodies. On top of that, there’s the massive climate impact of pumping all that oil.
In the past decade, engineers, scientists, and companies have been racing to find alternative materials that will be healthier for our planet and ourselves. Spider silk, mushroom leather, and a host of other innovations have all been hyped as the next big thing in sustainable fashion, but each have drawbacks. They can be expensive to brew in a lab, hard to scale, or just not very good at meeting the expectations of big producers or demanding customers. For Haverhals and Natural Fiber Welding, the solution wasn’t to invent a new fiber, but to hack nature to make use of what was already available.
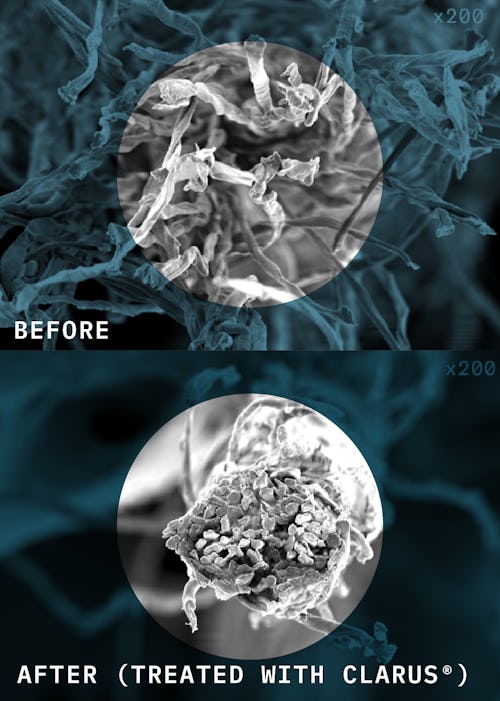
From Peoria, Illinois, where NFW is building its first industrial scale factory, Haverhals is trying to explain how the “welding” in NFW actually works. On the molecular level, the world looks like mountainous terrain. Over Zoom, Haverhals uses his fingers to outline imaginary mountain ranges. Only the very peaks of molecules come into contact with one another, with the valleys below never touching.
He offered another thought experiment. When we try to climb a wall, we don’t stick like Spiderman because the tips of our fingers can’t develop enough attraction to the molecules of the wall. But while conducting research at the U.S. Naval Academy as chemistry professor in fall of 2008, Haverhals observed how geckos use skin flaps to increase the surface area of their hands by 40 percent. Human fingers are only making about 3 percent contact, but when you increase it to gecko levels, those weak molecular and atomic forces that make things stick together start to kick in. Geckos don’t have glue on their hands — it’s just the chemistry of the hands. Haverhals decided to apply the same idea to fibers and search for a way to make them stick together.
With this idea in mind, Haverhals developed an ionic solvent bath that changes the chemistry of natural fibers by jerking their electrons into alignment. This is the core of his Clarus technology, which Haverhals turned into a business in 2015. Cones of yarn are dipped in a solvent bath while being wound and rewound through Haverhals’ machine, sort of like an old VHS player. The liquid solvent is then recovered in a closed loop system and can be used indefinitely, thus eliminating waste. Any type or blend of cellulose-based fiber can go through this process to make it more like its synthetic cousins. In this way, delicate merino wool, organic cotton, and even hemp can all be transformed into high-tech fabrics fit for olympic athletes.
The result of NFW’s process is a “new morphology, a new shape” on the molecular level, Haverhals says. “Nature reformatted.”
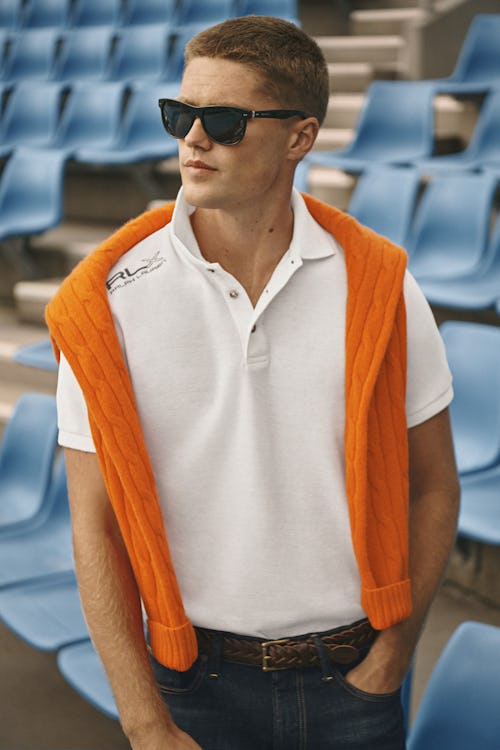
According to third-party tests, the technology makes natural fibers perform better than synthetic competitors. The breathability, moisture absorption, and dry-rate of a shirt made of Clarus Cotton is comparable to, or better than, any of the major technical apparel brands, and leaps and bounds above shirts made from regular cotton. In one test, a cotton canvas shoe’s upper made with Clarus was found to be almost twice as strong as synthetic uppers and four times more resistant to dry abrasion.
With $85 million raised in a series B round of investment, it's clear that business and industry experts are betting that Natural Fiber Welding is going to change fashion for the better. Sustainability leaders such as Sara Hayes, director of Materials Development of Patagonia, are backing NFW because of the fibers’ “enhanced performance,” which she calls “an exciting and very innovative technology with potential for high impact in the industry.”
Natural Fiber Welding is also catching on with brands you wouldn’t typically associate with sustainability commitments, from auto-maker BMW to luxury fashion companies like Richemont. Even uber-preppy Ralph Lauren is getting in on the action, releasing a special polo for the 2022 Australian Open made using Clarus.
“It reimagines one of our most iconic, timeless products,” a representative from Ralph Lauren says, “utilizing a first-to-market patented platform to transform virgin and recycled cotton in ways that were never before possible.”
The benefits of using Clarus extend beyond the life of any individual product. While synthetic performance fibers will take hundreds of years to break down, a garment made of NFW’s Clarus can naturally biodegrade in the same timespan as any cellulose-based fiber — or it can be recycled into new fabric.
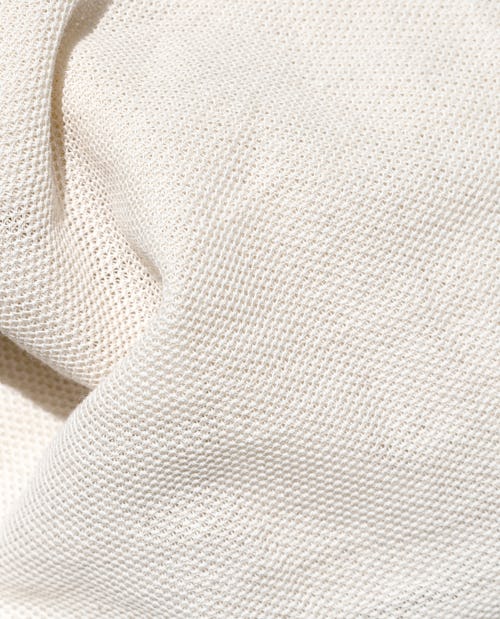
“Clarus has the potential to be impactful because it involves treating natural or recycled natural fibers in a way that gives them the performance capabilities of synthetics without the same problematic end of life,” says Dr. Amy Congdon, chief design officer at textile research group Biofabricate. For Dr. Congdon, this sets it apart from recycled synthetics like Prada’s Re Nylon. It may sound like a good idea to make crossbody bags out of old fishing nets, but what happens to the bags when they’re worn out and can’t be resold on Grailed? They likely wind up in a landfill. Even when it works, recycling is merely a temporary solution to an ever-growing plastic problem.
The story of Natural Fiber Welding is still in its first act. Industrial production takes years of patient tweaking and long-term investment, but so far, the early results are incredibly promising. For decades, the fashion industry has been churning out cheap synthetic fabric, and consumers have only been too happy to buy it. But as the consequences of all this plastic clothing become more clear, the need to change the way we make (and buy) clothes has only become more urgent.
For Haverhals, the solution has been in front of our eyes the whole time. The natural world is fueled by a freely available resource, the sun, and produces enormous amounts of fiber. “Photosynthesis is so much more wildly abundant than anything the petrochemical industry could ever dream about doing,” Haverhals says. He traced a circle with his hands, as if to encompass the globe. Each day, scientists estimate that Earth produces about half a billion tonnes of plant matter through the magic of photosynthesis, far more than what humans can synthesize from oil and coal in a whole year. With a little molecular zhuzhing from NFW, Haverhals thinks those natural plant and animal-based fibers will finally get their due.