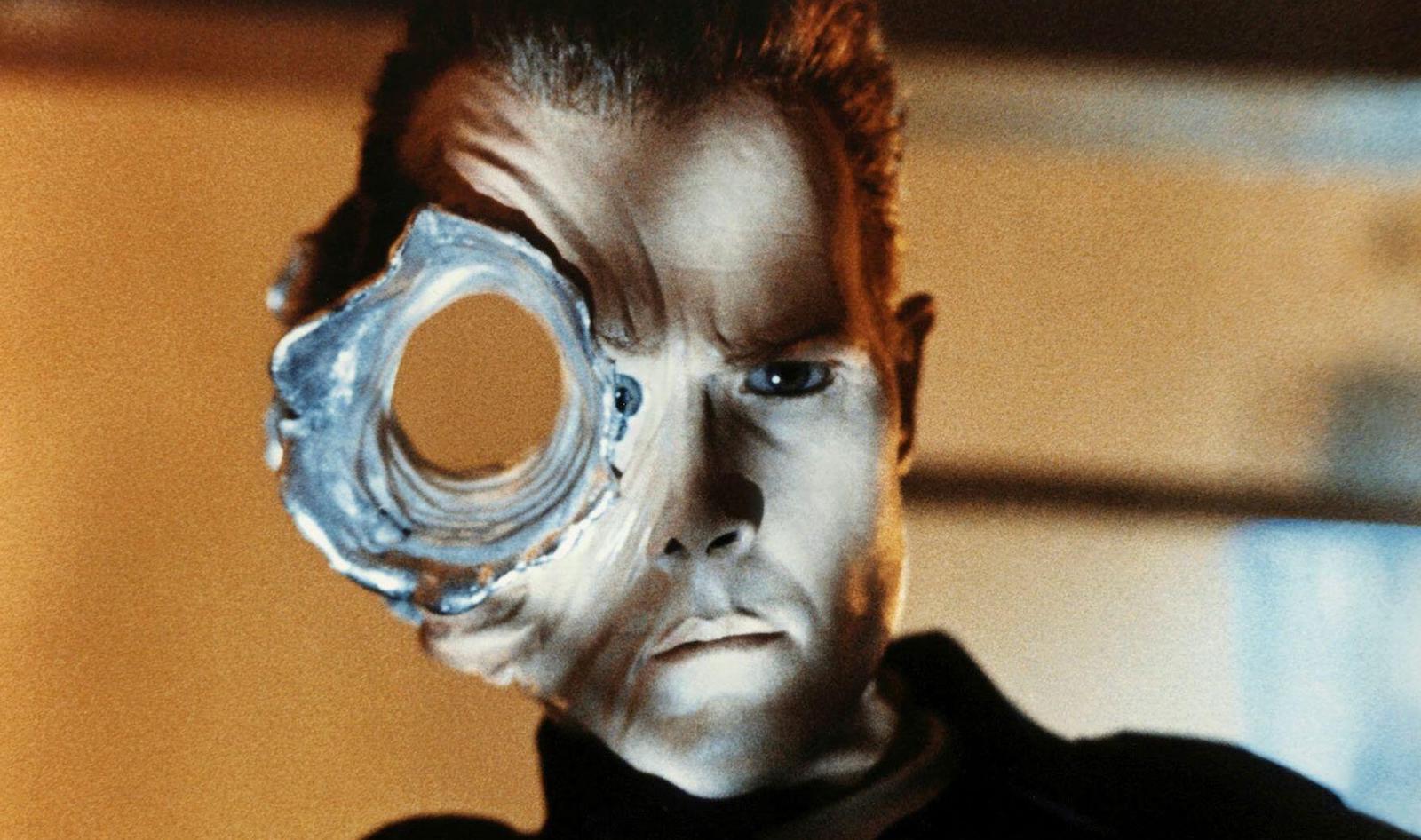
For the first time, scientists have spotted metal healing itself after cracking — an observation that could pave the way for the creation of structures and robots capable of mending themselves.
But for those worrying about the rise of real-life Terminator robots — don't: The newly discovered mechanism only works on a few metals and on incredibly small scales — at least, for now.
"Of course, there are lots of industries whose product engineers would love to translate this finding into intentional engineering approaches to create metals that automatically heal themselves in our structural applications," lead-author Brad Boyce, a materials scientist at Sandia National Laboratories in Albuquerque, New Mexico, told Live Science. "Self-healing metals could be useful in a wide range of applications from airplane wings to automotive suspensions."
Related: Real-life 'Terminator 2' robot can melt to escape jail, then solidify on command
Scientists had previously assumed that metals were incapable of repairing themselves, but the new discovery, made inadvertently by scientists studying nanometer-size chunks of platinum and copper, overturns this conclusion.
Metals sustain fatigue damage from repeated stress or motion, creating growing webs of microscopic cracks that can lead to catastrophic failures of jet engines, bridges and other vital structures.
But not all materials break under repeated strain: Some modern polymers and even ancient Roman concrete have been shown to repair their microcracks over time.
In 2013, a team of researchers used computer models to show that metals may also be capable of performing the healing trick, but they were not able to study metals at the tiny scales necessary so couldn't get any real-world evidence.
In the new study, published July 19 in the journal Nature, scientists investigated how nano-size metal pieces respond to repeated stress using a device called a transmission electron microscope. The device applied an extremely small force — equivalent to the stomping of a mosquito's leg — in the form of 200 tiny tugs to the metals every second.
In two of the metals, copper and platinum, cracks appeared and grew throughout the materials. But then, after 40 minutes, the metals fused themselves back together, leaving no trace of the cracks.
According to Boyce, the explanation for this miraculous self-repair lies in a process called "cold welding."
"In a nutshell, at the nanoscale, the local conditions around the crack tip are such that the two crack flanks are compressed into one another," Boyce said. "When they contact, the two flanks heal back together in a process that metallurgists refer to as 'cold welding'. This process does not appear to happen all the time, but only in cases where the local conditions induce crack flank contact."
How widely implementable the researchers' new observations are remains unknown. Firstly, to observe the cold welding processes, scientists isolated the metals within a vacuum so that no atmospheric atoms interfered with the equipment. This means they don't yet know if the process works only in a vacuum or not.
Similarly, the range of possible metals that can self-repair is also unknown. The scientists only observed cold welding in platinum and copper, but whether commonly used structural metals such as steel also perform the feat is yet to be seen.
There is also the problem of scaling. The metals used were tiny and highly ordered in their structures; whether large metals can be coaxed into healing too isn't known.
Nonetheless, the scientists are cautiously optimistic that their discovery could lead to fundamental changes in the way we build and design metal structures for durability, and could even have applications for spaceflight, where atmospheric particles are not a problem.
"Actually, we believe that this process may already be happening to some extent even in the ordinary metals and alloys we use in our daily lives — at least for subsurface cracks that are not exposed to oxygen, and possibly even for surface cracks," Boyce said. "To take full advantage, however, we can begin to think about material sections and microstructural design."