In a cosy home in Copenhagen, Denmark, hangs a wooden surfboard. It occupies pride of place among souvenirs from around the world. This board was created in Kovalam, on Chennai’s popular East Coast Road. And the artist? Sekar Patchai, a national surfing champion and now, also, a surfboard shaper.
“Travellers order boards from me to take it back to their country and hang it up in their homes as a reminder of their time in Kovalam,” says Sekar, who picked up surfboard shaping last year, after which he launched Kove Krafts along with his champion surfer girlfriend, Shrishti Selvam.
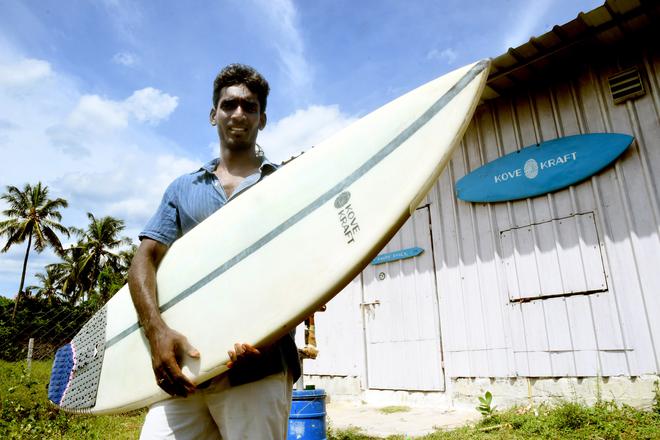
It’s 6pm, and Sekar has finished surfing and training for the day. Hitting play on his phone, he settles down at his workshop in Kovalam fishing village as ‘Moongil Thottam’s beats fill the space. Surfboard shaping is a meditative and calming process for him. “It’s easy to get immersed while shaping. My favourite part of the process is reducing the block of foam to a nicely shaped board. I’m completely in my zone when I’m listening to music and creating with my hands,” adds Sekar, who makes boards out of EPS foam as well as balsa wood.
For almost all the local surfers from Covelong, procuring a surfboard was a challenge when they started out about a decade ago. The sport was nascent in India, and surfboards were tough to source. “We were only able to buy them from those coming from abroad. That is why I started shaping so I could make boards for myself,” says Sekar.
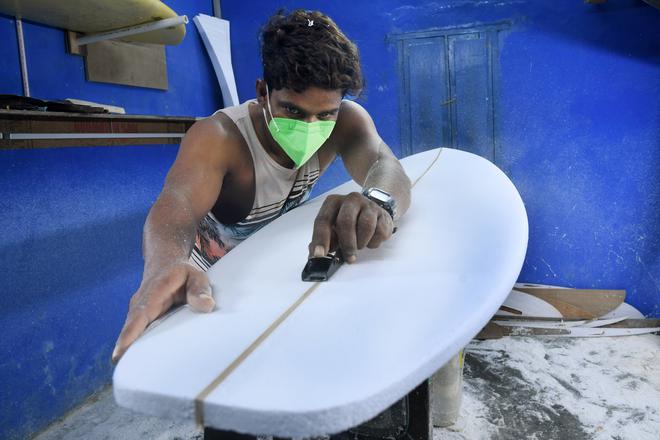
In 2012, when Australian surfer Dave Hearns visited India and shaped a board during his stay in Kovalam, he became an inspiration for surfers like Sekar and Santhosh Moorthy. Santhosh, who is one of India’s first shapers, was a stone carver in Mamallapuram for six years. He spent his days fishing and carving intricate shapes on stone, which he then sold from his cousin’s store.
Things changed when Dave saw him surfing using a block of wood, and gave him his surfboard to practise with. “As a thank you gift, I made Dave a small stone pendant in the shape of a surfboard. That’s when he suggested we should start making surfboards in India,” recalls Santhosh. As a result, Temple Surf Boards was born in 2014. It had a good run before shutting down a few years back. Dave went back to Australia and eventually, Santhosh launched his own brand, Alai surfboards, in 2019. “My stone carving skills come in handy in this profession,” he says, adding “They help me understand symmetry and shine.”
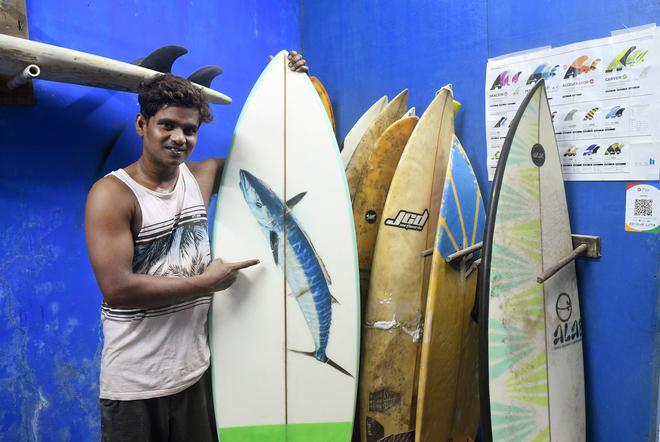
Surfboard shaping is still purely a handmade business in India. Though the demand for boards is picking up as surfing gains popularity along the coast, it is still not big enough to warrant setting up factories where they can be mass produced. Surfboards here are created on a made to order basis, with some of them making around three a month. They are competitively priced, with shapers charging anywhere around ₹17,000 to ₹25,000 and upwards (barring Bali in Indonesia, prices abroad can start at ₹70,000 and go upto a lakh or more).
Creating a board can take between 15 to 20 days depending on the specifications requested by clients. Some even ask for elaborate art work or their initials. “It always helps to watch a video of them surfing to get a better idea of their surfing ability. Factors like the surfer weight, height and their performance level influence the final measurements of the surfboard,” says Sekar, for whom the most challenging part is fixing the fin plug system into the board. The fins play a vital role in the speed and direction of the board so it is important that they are perfect.
“Now, there are CNC (Computer Numeric Control Device) machines that can cut the foam to the desired shape. It’s faster, easier, but maybe still early for the India market,” says Peddy (otherwise known as Pandurang Pednekar), who owns Bebo boards and school, and creates standup paddle (SUP) and surfboards out of his rooftop in Mandrem, Goa. SUP boards are longer, wider and thicker than surfboards.
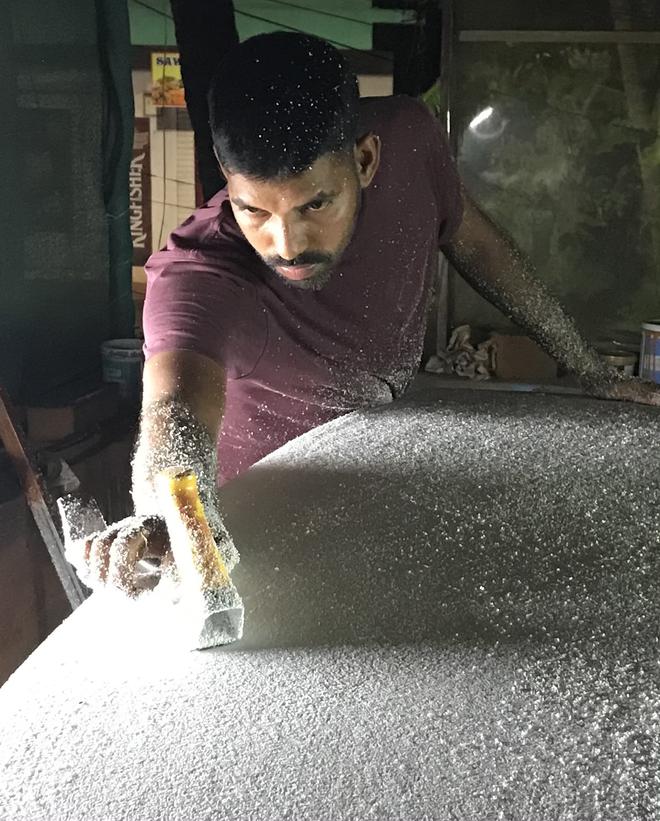
A former fabrication structural engineer in the shipbuilding industry, he got intrigued by boards when he saw a group of stand up paddlers in Goa. “It looked like they were standing on water. And I just had to know what the technique was and wanted that board for myself. That’s how it all started,” says Peddy, over a call from Goa.
Of all his creations, he says he is particularly proud of the hydrofoil (an underwater fin that helps move a boat or in this case the board) wind surfing board he made. He believes those can be game changers in terms of speed. “I am making a SUP board with hydrofoil for myself now,” he says.
There is an undeniable charm about handmade boards, agree the shapers. Further down Tamil Nadu’s wave-rich East Coast, Samai Reboul,who started the Kallialay Surf School with his brother from their home in Auroville, says he has been making surfboards since 2012, and even now some of them may not be 100 percent perfect. “Handmade surfboards are rare abroad,” he says.
Samai launched his surfboard brand Kallialay Original Series (KOS) in 2019. Prior to that he was making them with another enthusiast under a different brand name. “But now, it’s a one-man show,” says Samai, who like most others, got into shaping given the lack of availability of boards in India. He learnt the skill from a few from French shapers.
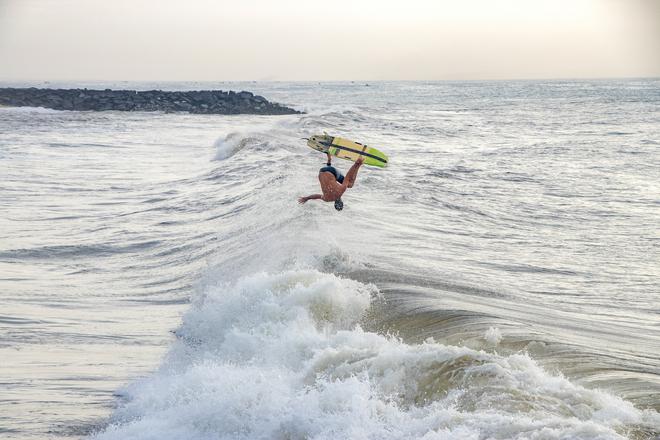
“This is a passion project of mine,” says Samai adding that his day job is surfing coaching. By evening, “time and vibe permitting,” he goes to his unit in Auroville to shape. It is not a process that he wants to rush through and put together under stress or dictated by time. “I have stopped taking orders. And I have hiked the prices by 50 percent, so for every two boards I make, I can make a free surfboard for upcoming talents,” he explains. Since 2020, Samai has made 24 boards. While his clientele, like the rest, is a mix of Indian and foreign surfers, he prefers to create boards for local clients.
For some of these self starters, it has been a steep learning curve. Sekar, who has completed 15 boards so far, says the first one he made was for his girlfriend for her birthday. But disaster struck as he used polyester resin instead of epoxy resin. The wrong resin melted the foam. After a lot of trial and error, with just one night in hand, Sekar sat through the night and made another surfboard, just in time to gift it to Srishti the next morning.
Peddy says the first board he made failed because of its weight. “It was made with PU foam instead of EPS foam. The paddler had to put in a lot of effort to manoeuvre it,” he says. While Peddy was initially self taught, he later mastered his techniques with a Swiss shaper, who was invited to India by Cedric Reynard, a SUP instructor from Switzerland, who surfed with Peddy in Goa and saw his work.
This kind of camaraderie among the surfing community is something Peddy values as much as the other surfers. They are always learning from each other, bouncing off ideas and helping each other improve. And that is what Peddy and the shapers want to do with their handcrafted boards: help surfers enjoy and excel at riding waves.