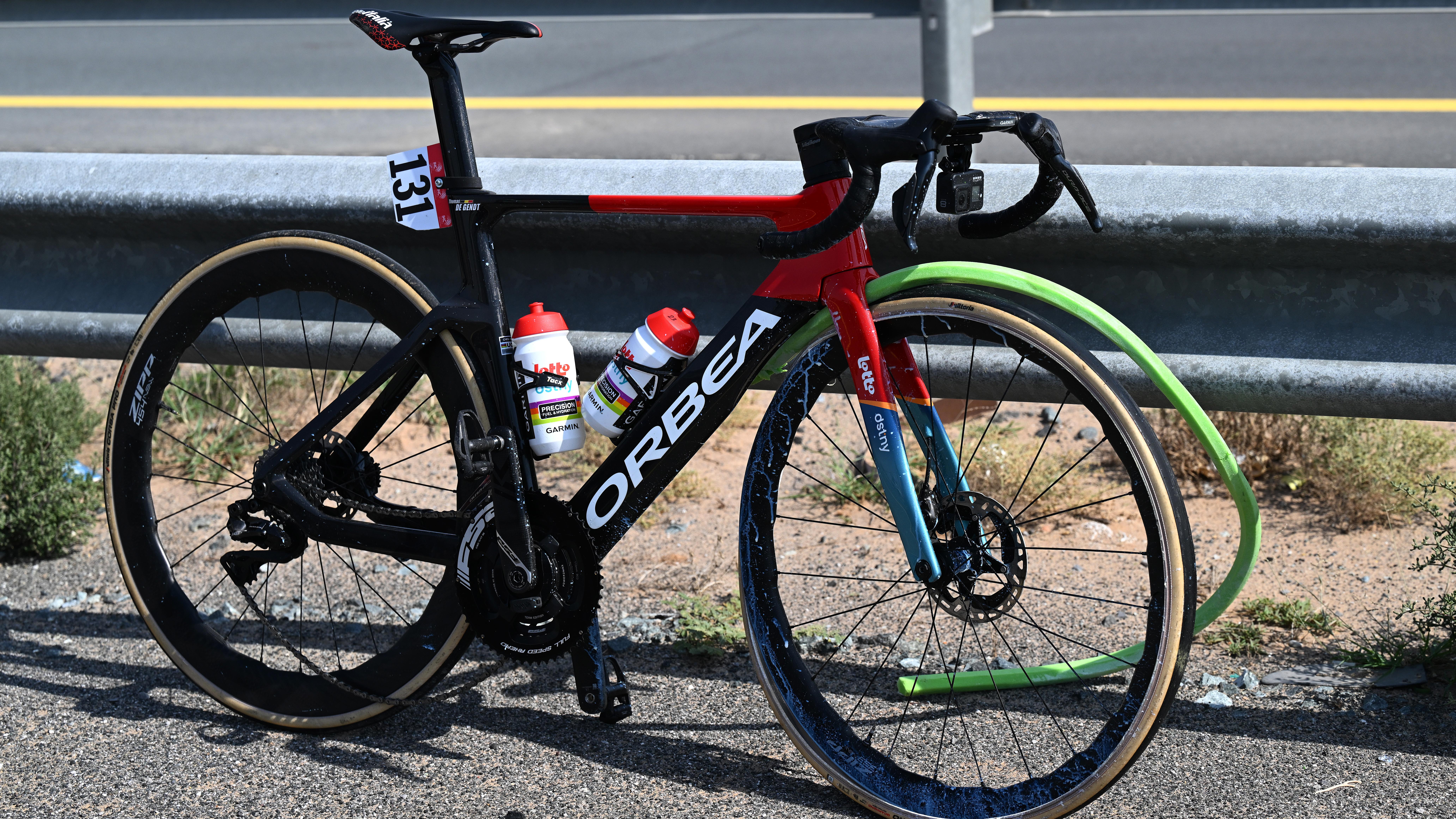
Over the last few weeks we've seen a range of discussions calling into question the safety of hookless wheels. Although we've seen the discussions before, when Lotto Dstny's Thomas De Gendt crashed at the UAE Tour they were suddenly relevant again. Images of the bike propped against the roadside barrier, with the front tyre off the wheel made for a dramatic point of reference.
With a lack of explicit evidence, theories abounded. De Gendt claimed to have hit something, and both Vittoria and Zipp blamed an errant rock, but the conversation instead focused on the safety of hookless wheels. With no proof it seemed natural to wonder if the tyre had simple come off as a result of the design. Although Cyclingnews has since obtained images that show the rim was subject to an impact, there are still reasonable questions to answer about design and production of hookless wheels.
Are brands playing fast and loose with safety? Or is there change needed with the standards and recommendations from ETRTO (European Tyre and Rim Technical Organisation) and the ISO (International Organization for Standardization)? This is a discussion with six brands, including Zipp who's wheel is at the forefront of the current controversy, taking a look at the facts. Is there really a safety factor of 1.1?
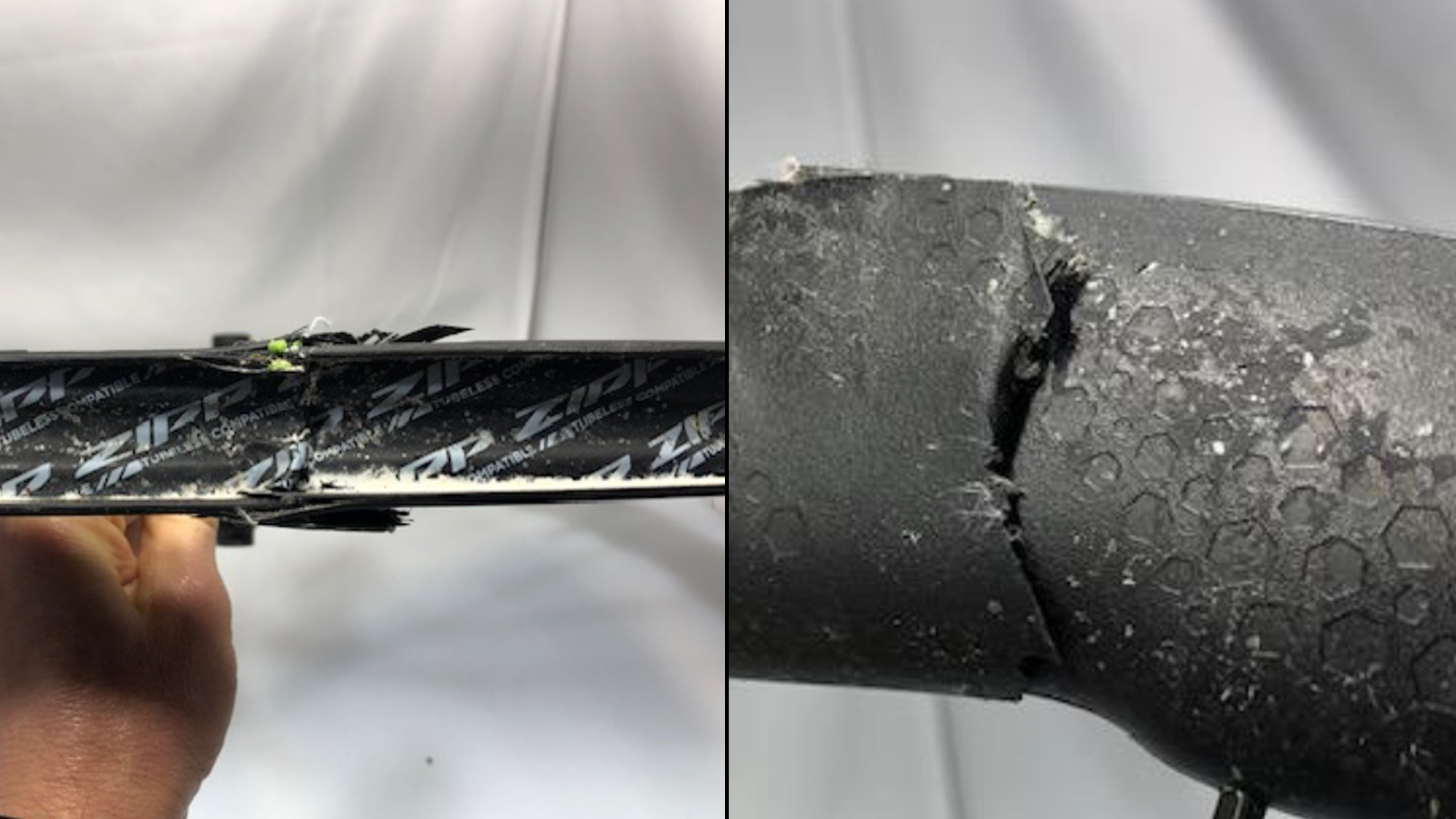
What is the controversy?
Although the ETRTO made changes to the recommendations for compatible tyre and wheel sizes with hookless tubeless systems last year, it wasn't something that garnered widespread attention. De Gendt's crash though, kickstarted the conversation again. Although no one knew what happened, speculation was that the tyre came off at random and it was common to see the number 1.1 thrown around. That number refers to the ISO test for tyre retention. Jake Pantone, VP of Product and Brand for Enve Composites, explains what that is. “[You have to] inflate the tyre to 110% of [or 1.1 times] the maximum pressure of the wheel system and maintain that air pressure for a minimum of five minutes.”
This test is also something that CPA President, Adam Hansen, referenced in his discussion with Velo. In that article, author Shane Stokes writes "[Hansen] mentions that with hooked tyres, the ISO standard says the pressure limit is 1.5 times the maximum stated PSI." Stokes then goes on to quote Hansen as saying "What that means is that on a clincher hooked rim, normally the max psi is 120. Under the ISO standard, 1.5 times 120 is 180 psi. So if you put 180 in there, it’ll pop off. But for some reason, the hookless standard is just 1.1. I don’t understand why they have changed the bar on the hookless system. I’d like to ask if they changed the bar on the hookless system because the tyres cannot stay on if it’s at 1.5? If the ISO standard is 1.1, that means that if the psi is set to 73 as a maximum, the tyre can come off the rim any moment if pressure increases to 81 psi.”
Given the ISO rule, Hansen is asking a question that makes sense. It's also a question relevant not only to professional riders but also to consumers who purchase wheels. It's especially relevant to anyone who needs to run pressures that approach the maximum.
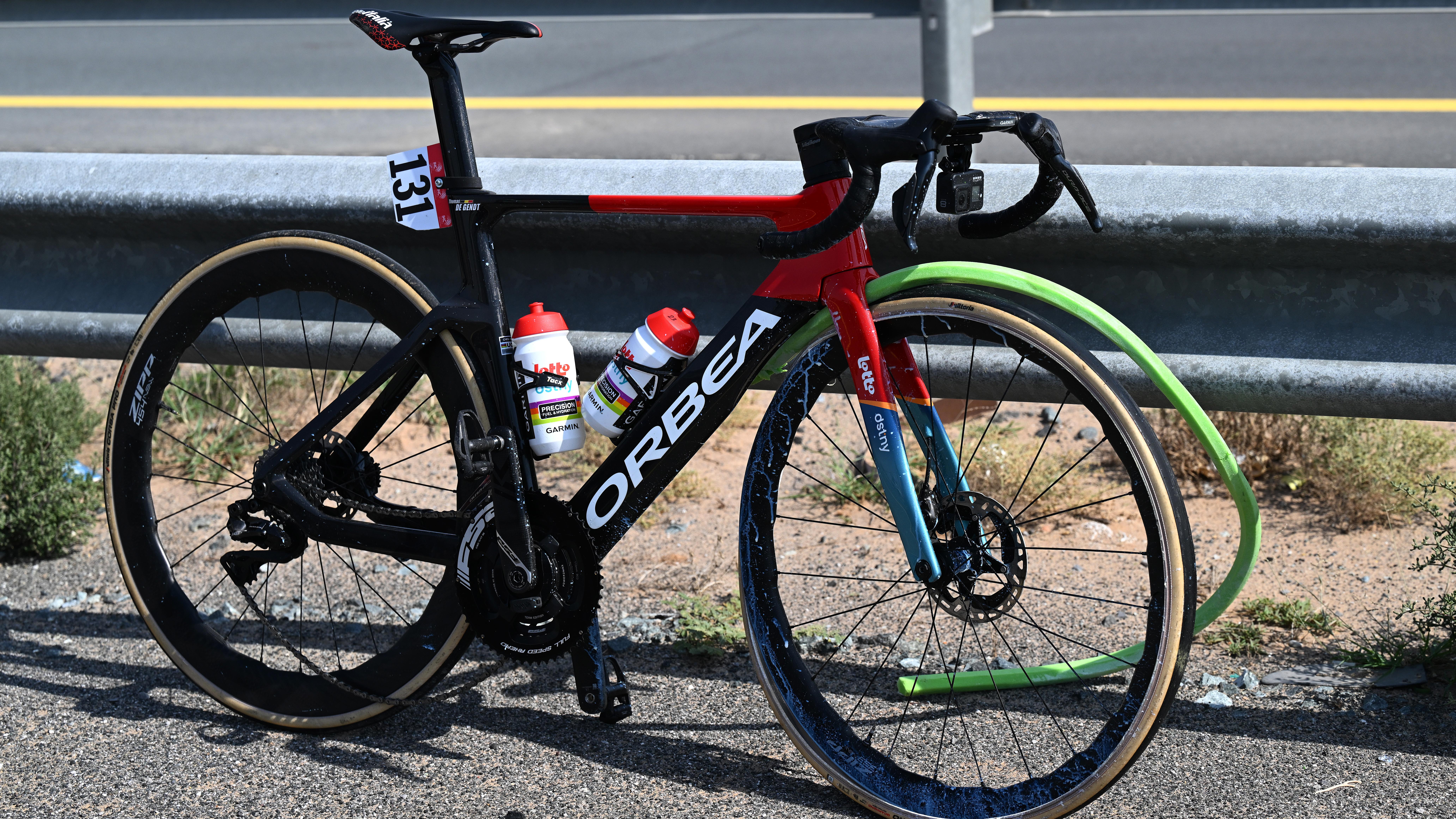
Do wheel companies follow the ISO test?
There are a number of companies who have already fully transitioned to hookless wheel designs and some are more transparent than others. One of those brands is Cadex which has been producing hookless wheels alone since re-entering the market in 2019. During that time, Cadex has advised consumers to only use approved tyres. Cadex is also one of the brands that's most transparent about the tyre testing procedure it uses.
Any tyre on the approved list for Cadex wheels goes through two types of testing. The first is a high-pressure tolerance test. The brand told us that during this test, "the tyre is inflated to 72.5 psi (5 bar), an average minimum pressure for most riders on 25c tyres, and must withstand this pressure for 24 hours without blowing off. Next, the tyre is inflated to its recommended maximum pressure and must withstand this pressure for 24 hours without blowing off. After that, the tyre is inflated to 1.2 times the recommended maximum pressure and must withstand this pressure for 24 hours without blowing off. Finally, the tyre is inflated to 1.5 times the recommended maximum pressure and must withstand this pressure for 24 hours without blowing off."
You'll notice that Cadex references a 25mm tyre because Cadex wheels use a narrower 22.4 mm internal width, which is compatible with a tyre that size. You'll also notice that Cadex pushes to 1.5 times the ISO test for a time frame of 24 hours. Cadex explains that number comes from a desire to "simulate such extreme conditions as hitting a square edge or a pothole at high speed causing the tyre pressure to increase suddenly."
Going even further beyond the ISO test requirement, Cadex also uses a high-pressure braking test. During that test, the "tyre is inflated to 1.2 times the recommended maximum pressure, mounted on a disc brake wheel and must withstand braking forces without blowing off or experiencing a shift in position of more than 3mm." Cadex goes on to state that the reasoning behind the second test is "to simulate accidental high-speed uncontrolled braking causing excessive friction between road and tyre and possible movement of the tyre on the rim resulting in blow-off."
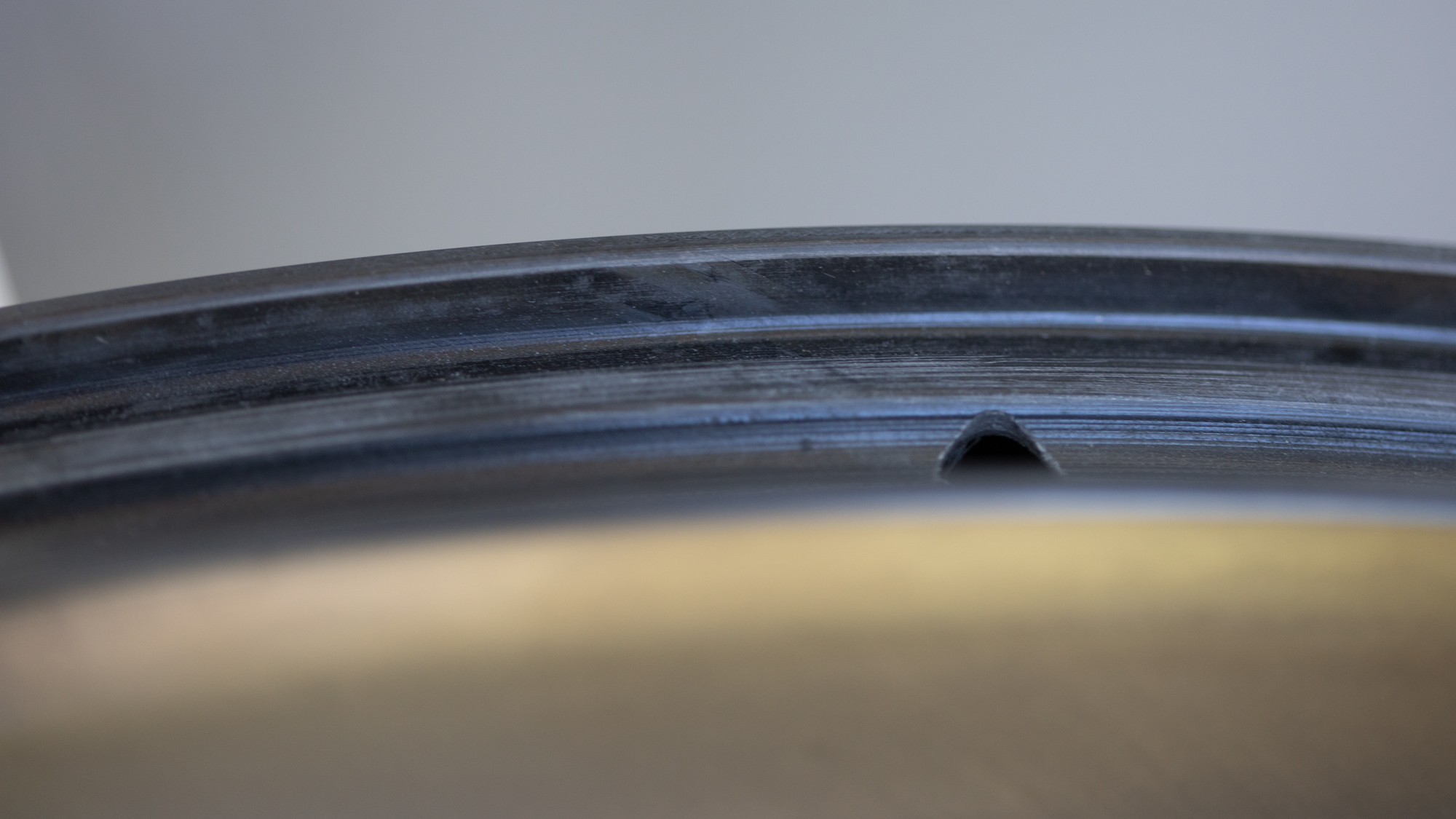
Clearly, Cadex is going well above and beyond the ISO test but the brand is not alone in that. Cyclingnews also spoke with Jake Pantone, VP of Brand and Product and Enve, who outlined the brand's tyre test by sharing that it starts with three copies of the same tyre for multiple tests on every size. This means that "if a brand makes three sizes (25, 27, 29) of model “TT”, we test nine tyres" and each test occurs on an ENVE SES test wheel with a 25mm internal width.
With the wheels and tyres ready, each test is a multi-step process. The first step is to "inflate the tyre to maximum Enve rim pressure of 80psi/5.5bar and 'pressure soak' for 24 hours." Pantone notes that this is essentially the ISO test but extended from five minutes to 24 hours. After 24 hours, Enve measures the tyre’s height and width, then removes the tyre and "measures bead stiffnesses for both beads and bead diameters of both beads."
With the initial steps completed, the same tyre begins the next steps. That starts with reinstallation and inflation back to 70 psi. Once reaching 70 psi, "pressure is increased in 10 psi increments every 10 seconds" and this continues until either hitting 160 psi or experiencing blow-off.
With the test complete, Pantone explains that the "acceptance criteria for a tyre to be listed as approved/recommended for use on an ENVE hookless rim is 120 psi or 165% of ETRTO max stated pressure of 72.5 psi." Again, he adds context saying "we’ve been doing this test much longer than there has been this ETRTO max pressure. All our 25mm-internal hookless rims are actually qualified and rated to a max pressure of 80 psi, while our 21-23mm internal width rims have a max pressure rating of 90 psi. When we perform the above test on a narrower 21-23 mm internal rim, our acceptance criteria has historically been 135 psi or 150% of 90 psi. If we convert the 135 psi acceptance criteria to a margin of safety off of the new ETRTO 72.5 psi, then the percentage is 186%."
Another brand that has been a more recent adopter of hookless technology is Hunt. Although Hunt has the 32 Aerodynamicist UD wheelset, the latest Hunt Sub50 wheel adopted this design as well. Hunt states that hookless allows the brand to "slightly reduce rim weight, improve manufacturing consistency, and improve aerodynamics." Hunt, like Cadex and Enve, also has a test that far exceeds the ISO test; however, like Enve, the brand starts with something similar to the ISO test.
Hunt explains the process by starting with a general statement saying "It is our normal engineering practice to test all our wheels, both hooked and hookless, using our Design Validation Plan (DVP), as developed by our engineering team." The brand then goes on to say "For tyre retention, the ISO 4210-7 greenhouse effect test and overpressure test are used." That starts with "a wheel with an inflated tyre heated to 80 C for four hours. The wheel is measured before and after to ensure it is geometrically comparable." Then the "overpressure test for ISO 4210-7 sees the tyre inflated to 110% of either the maximum pressure of the tyre or rim (whichever is lowest), for five minutes." From there, the brand adds an additional test "which is the same test as the ISO overpressure test, however, we inflate the tyre to 150% of the stated operating pressure used in the ISO test."
Like Cadex, Hunt also performs a test beyond the pressure tests. According to the brand, "a rolling road test (RRT) is performed on every new wheelset as part of pressure testing, twice the number of 10mm 65kg loaded bumper strikes as ISO require which equates to 752,082 hits for ISO and 1,504,604 strikes for the Hunt Rolling Road test."
For Hunt acceptance means "before the wheels can make it to market, all wheels must pass these pressure-related tests. The pass criteria are that the tyre must remain intact on the rim and the tyre must not derail from the wheel or have permanent damage that prevents normal operation when inflated to normal operating pressure. "
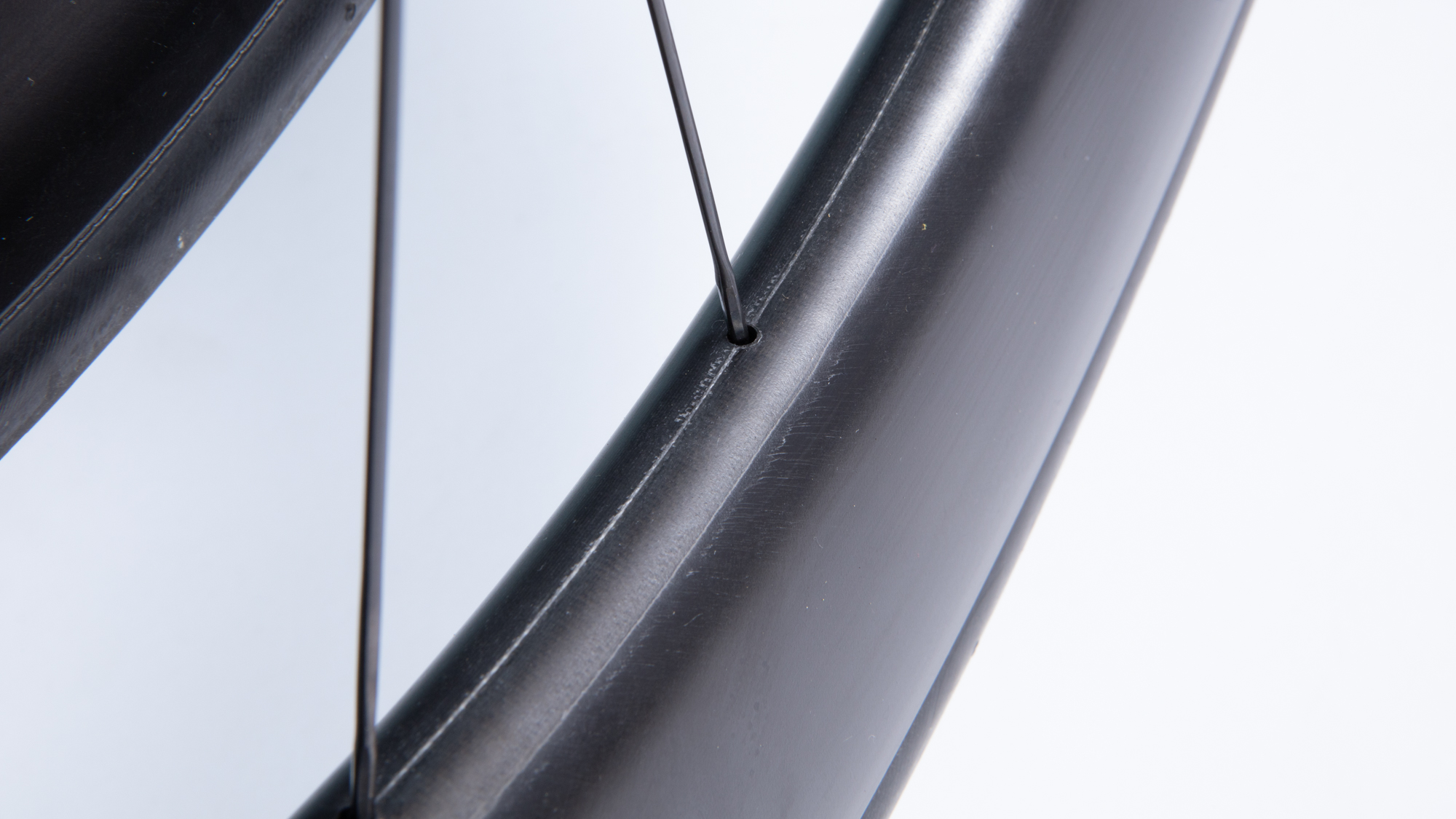
The importance of dimensional stability
According to Pantone, Enve has had conversations with tyre brands "and they voice frustration with other rim manufacturers who do not follow ETRTO. Given that geometry is critical in tubeless performance, it is critical that rim manufacturers take their rim dimensions seriously." He also explains that "hookless allows ENVE to make rims that strictly conform to these dimensional requirements."
In that statement, he's referencing the removal of silicone bladders from the production process. This leads to less variation in size but, hooked or hookless, there is always variation. Metal moulds wear and pieces shift during production. No manufactured part is exactly the same from part to part and that is why the ETRTO recommendations include a range of acceptable dimensions. What that really means though, is that once a brand designs a wheel, it must also have a robust quality control system in place.
For Enve, Pantone explains the QC process is "multiple steps and it starts at the mould level. The dimensions of the rim start with the mould the rim is coming out of. So, before we ever cut a rim mould, we make sure all the numbers that are programmed into the CNC machine are correct. Then once the mould is cut, we measure the mould. Rims are then made in the mould and the rims that come out of the mould are measured in the initial qualification process. Once a rim and moulds are in production, we are continually doing random batch testing of the rims, and there are cycle counts on the moulds to ensure they aren’t wearing out to the point where a rim’s dimensional integrity is compromised."
Pantone also gives greater context to the advantages of hookless wheels by saying, "This is the reality of 'why hookless'… the ETRTO measurement for bead seat diameter that we target is 621.95mm and we hold to that by +/- 0.2mm. Hookless makes this possible because we can use precision machined tooling to mould the rim. Like we’ve always said, carbon parts are only as good as the moulds that produce them."
I was also able to discuss dimensional stability with Hunt. When asked, the brand communicated that "one of the most important elements in the DVP is to perform a dimensional check. The wheels are measured to ensure they conform to the engineering drawings, which have previously been ensured to be ETRTO compliant. For each batch of production wheels, the critical dimensions for tyre retention are measured to ensure that the rim matches the drawing and is compliant with ETRTO specifications."
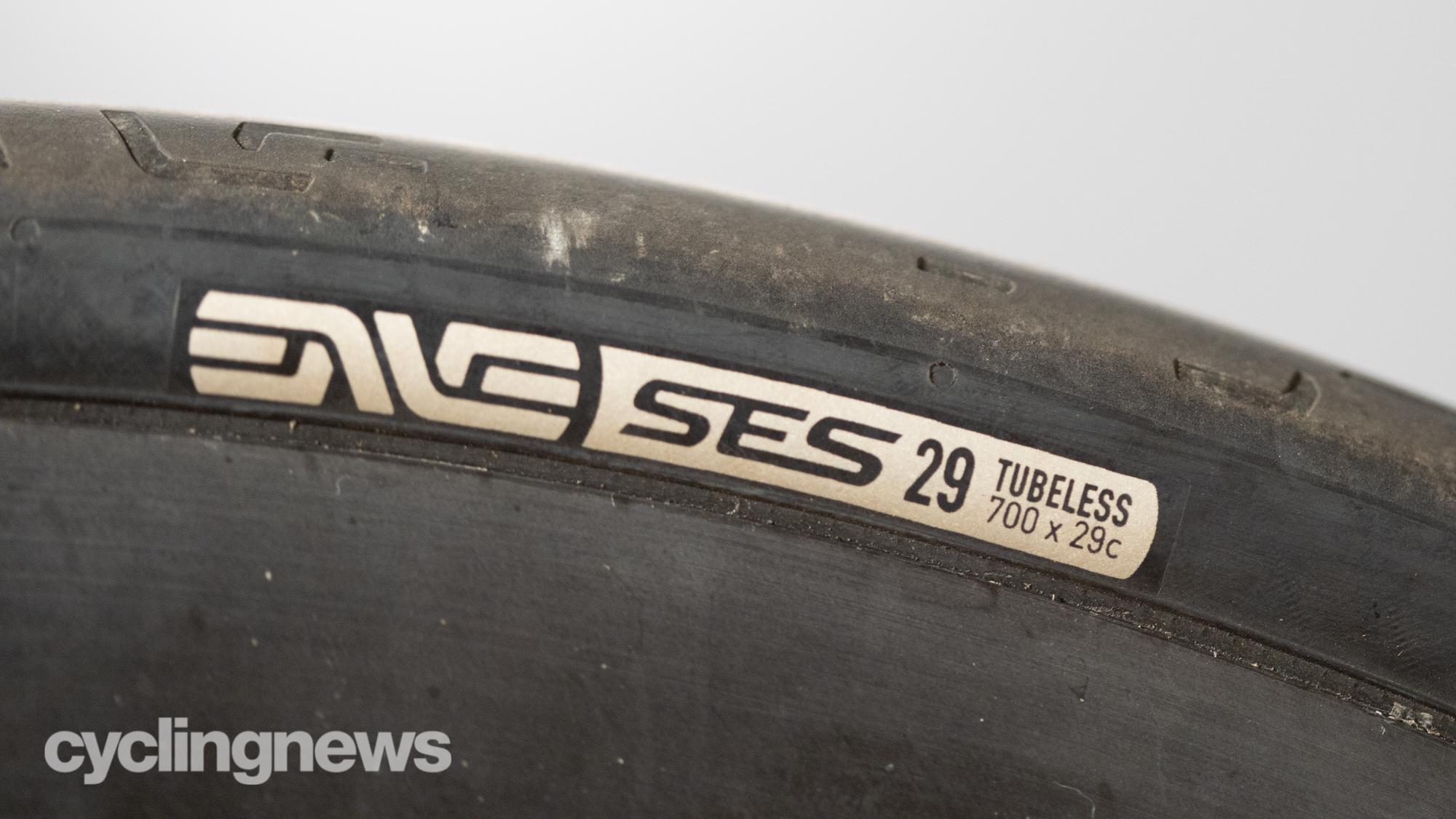
What about the tyre companies?
Wheel companies tend to be quite happy to share details about design and testing. In contrast, tyre companies do not have a similar set of recommendations and are rarely willing to share any details. One brand that was open about the challenges was Rene Herse. According to Jan Heine, head of R&D at Rene Herse Cycles, the reason that tyre companies don't have recommendations is that "defining both parts of the system would put the ETRTO/ISO in the business of designing rims and tyres. By defining only one part, the ETRTO/ISO have no responsibility for ensuring compatibility—that falls to the makers. And since rims are solid compared to tyres (which stretch), it makes sense to define the rim, and not the tyre." This obviously points back to the importance of rim companies both following the ETRTO recommendations and ensuring dimensional stability over time.
Heine was also willing to share some details of the Rene Herse testing by saying "Among the many testing protocols for our Rene Herse tyres is a test for blow-off pressure. We make sure that the worst-case scenario, a rim that measures on the small end of the tolerances specified in the ETRTO/ISO standards, still keeps the tyre on the rim with a generous margin of safety beyond the maximum allowable pressure."
The only other tyre company that spoke directly about testing was Schwalbe. During my investigation of the updated ETRTO standards last year, I spoke extensively with Schwalbe product manager Felix Schäfermeier, and he was open and upfront about the testing Schwalbe does to make sure that wheels and tyres work together. Specifically, Schäfermeier was clear and happy to share that "the ISO derailing test is just an absolute basement test. This test is about inflating the tyre to 1.1 of the max tyre pressure for only 5min and [it's] easy to pass."
Unfortunately, as I write this follow-up a year later, I wasn't able to reconnect with Schäfermeier to further clarify. Instead, Jakob Maßen, also a Schwalbe Product Manager, did add more context by stating "For our [Schwalbe's] derailing tests we use 160% of the indicated max pressure for one hour. In our experience, not only the higher percentage but also the longer time period is critical to ensure safety for consumers."
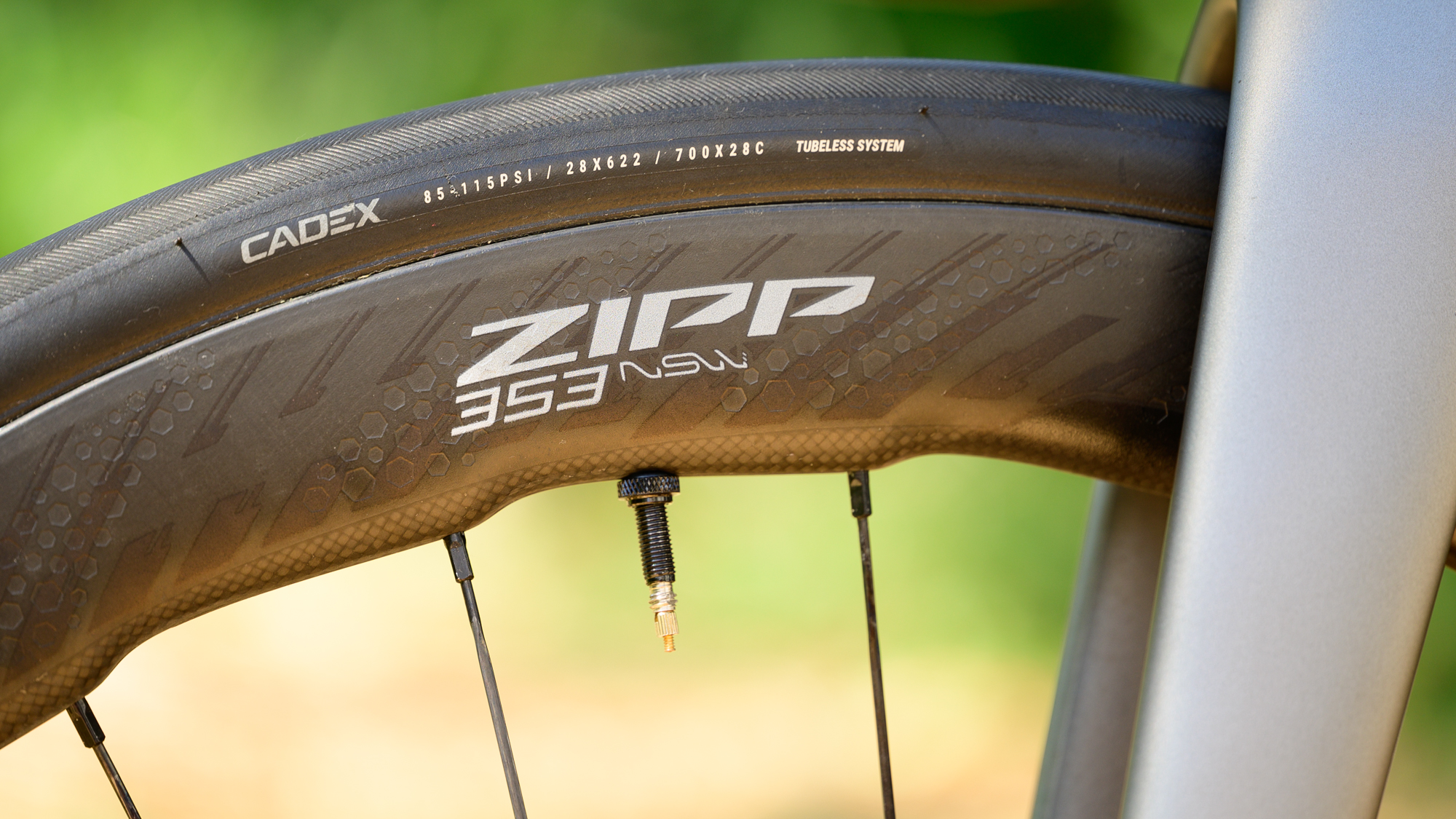
Zipp has a different approach
The Zipp 353 NSW that began this conversation had a tyre come loose because of an impact. Zipp commented on that and Pantone also spoke to the expectations around impacts by saying "broken wheels can’t be expected to retain a tyre. Tubes, tubeless with hooks, tubeless without hooks, and tubulars will all throw the tyre if the rim is no longer load bearing or breaks through the dimensionally critical tyre bed." However, Zipp is also a company that makes hookless wheels and faces the same challenges that other brands do.
As Enve and Hunt also shared, Zipp started by sharing that part of the advantage of hookless is that there are no soft parts needed in production. Nathan Schickel, Zipp Product Manager, told me that the moulds are all hard with no silicone pieces, and that helps keep dimensional stability very consistent throughout the lifespan of the mould. When it's time for a new mould, Zipp runs samples and then validates dimensional stability on the produced wheels. During the ongoing production run, the brand periodically pulls rims from production and validates dimensional stability. Schickel also shared that as the brand continues to further hone production processes, dimensional stability is always at the forefront. Production continues to evolve, dimensional stability gets better, and new designs do a better job of keeping tyres on rims with less waste.
When it comes to tyre testing though, Zipp takes a different approach. Like other companies I talked to, Zipp does run internal tyre tests. For Zipp that means inflating to at least 1.5 times the max system rating then holding it for 1-hour at each pressure increment. Again, far beyond the ISO standard test.
What Zipp does differently is that while the brand tests tyres internally, those tests don't inform the list of list of compatible tyres. Instead, as outlined on the SRAM website, "Tyre fitment is the responsibility of the tyre manufacturer." Rather than having a tyre retention test like Enve, Zipp makes a consistent envelope and it asks the tyre companies to test the wheels, then certify compatibility.
The effect of this approach is that tyre companies retain responsibility, and define their own tests, but without creating silos in the industry. In some ways, you can see an echo of what Heine shared but Zipp is a larger presence. Part of the reasoning behind this approach is to force the conversation and help create change within the industry.
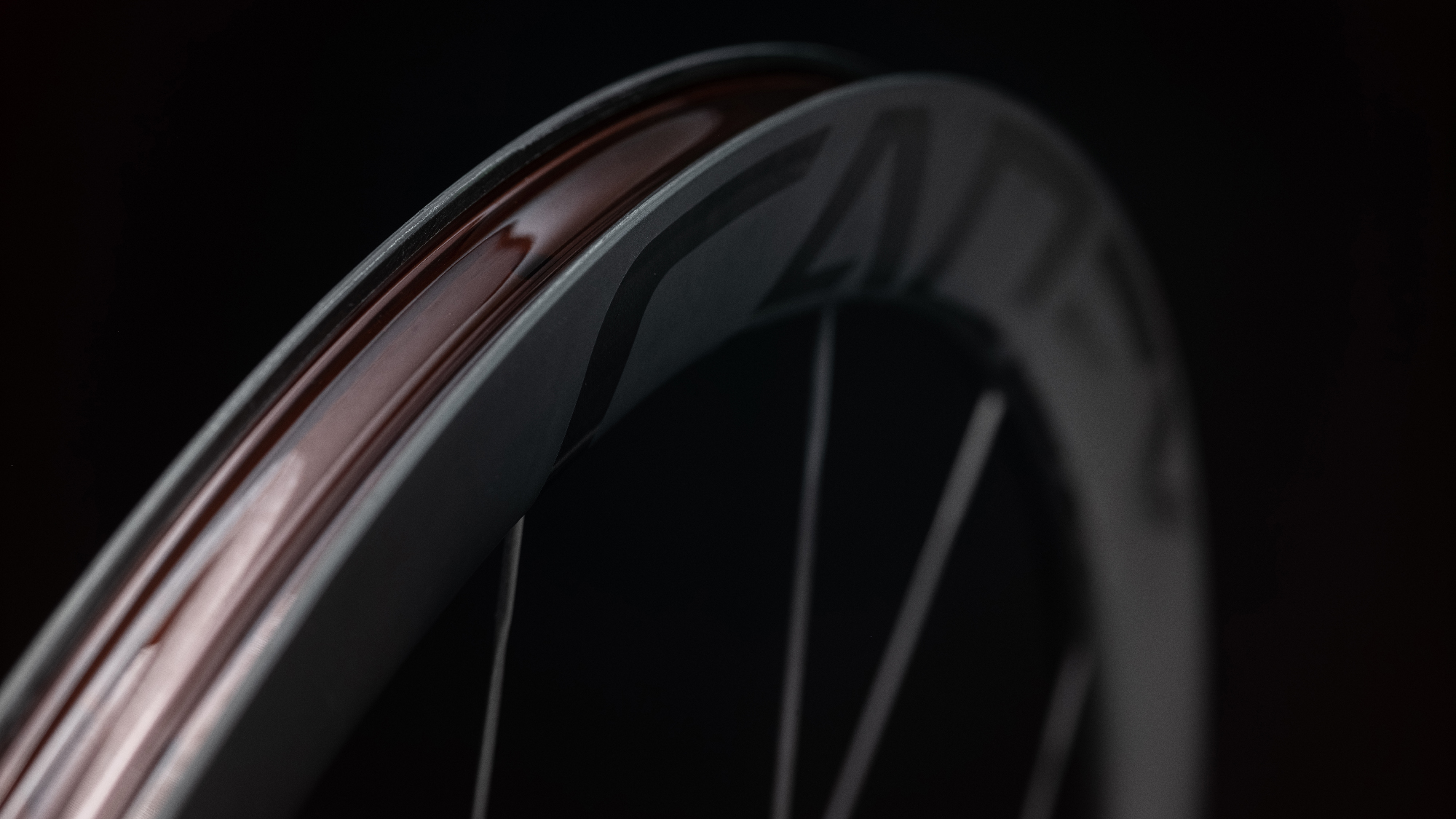
What comes next?
Reading through Hansen's comments, you can see that his frustration is with a perceived lack of standards. There are standards, but the brands that are creating some of the fastest, most capable, wheels available share his belief that those standards are not high enough, and they're already doing something about it. Hunt, Cadex, Enve, Zipp, Schwalbe, and Rene Herse are just six brands that we spoke to, and they all use tests that far exceed the minimum requirement. Schickel from Zipp was clear in saying "Zipp believes that 1.1 is not a viable safe standard" and Heine stated that the "110% blow-off pressure is a pretty weak standard."
With that in mind, better standards would be a good thing, but it may not actually change anything. The rest of the quote from Schickel is that "in Zipp's own testing, and in the conversations we've had with other companies about testing, everyone is testing above that 110%" while Heine goes on to say that since the current test "doesn't preclude anybody from testing higher, nobody spends any energy changing it."
As a consumer, what this all means is that it's important to choose quality products. As you look for your next set of wheels, consider the vendor. Do the wheels follow the ETRTO design guidelines? Is there a clear test protocol in place to ensure dimensional stability of the wheels during production? Do the tests exceed the ISO standard? If these processes aren’t in place, you could be putting yourself at greater risk.