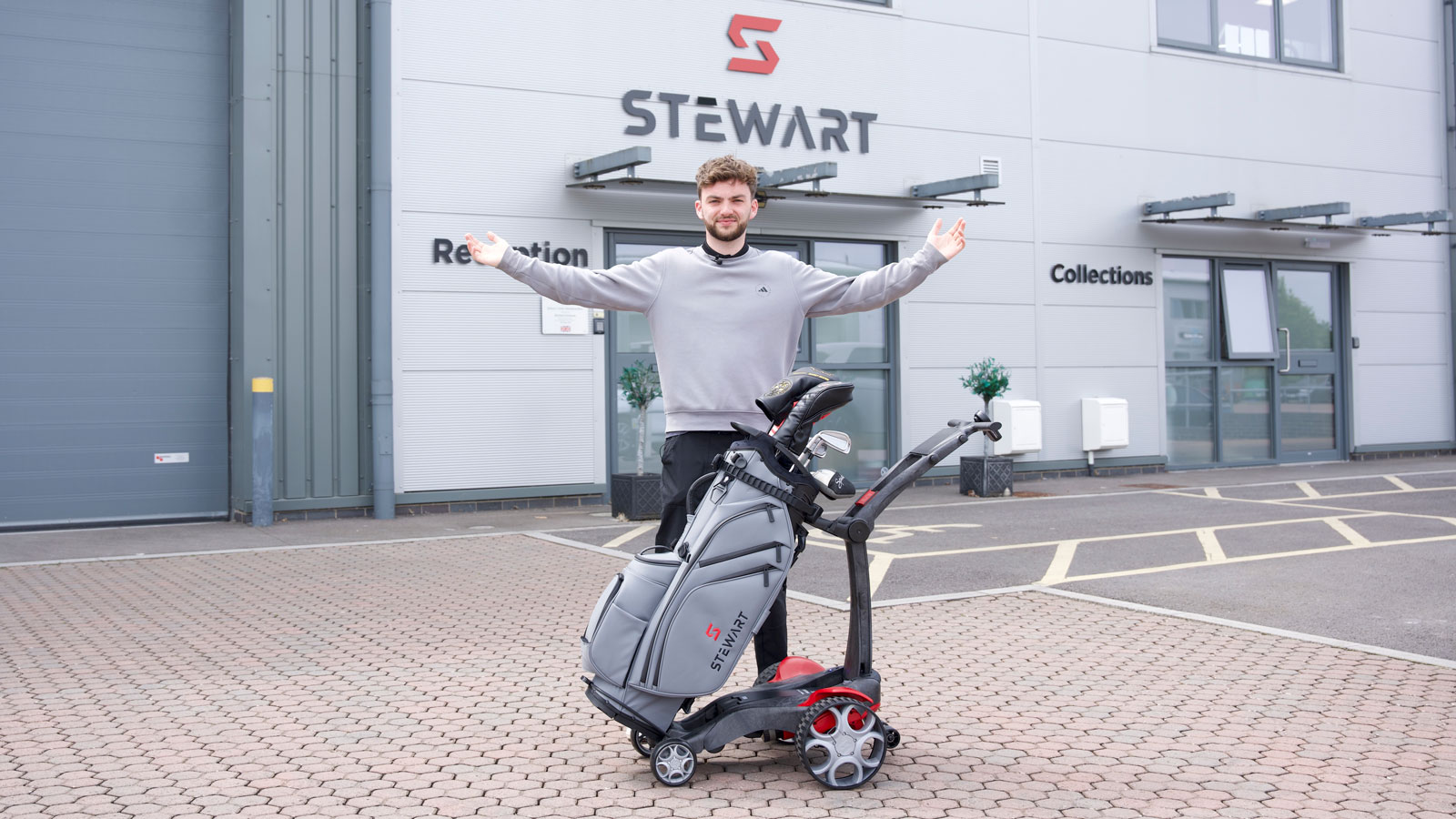
Have you ever wondered how an electric golf trolley is built? Despite the number of trolleys we've tested at Golf Monthly over the years, we were still none the wiser as to how they are actually designed, engineered and assembled before they head out onto the golf course.
Luckily for us, Stewart Golf, market leaders in designing and engineering remote electric golf trolleys, invited us down to its factory in Gloucestershire to see exactly how its 2025 Q Follow trolley is designed and built. Not only that, but we'd be helping out on the assembly line, too. The new 2025 Q Follow trolley has arrived with improved 8th generation Follow technology, greater customisation with six new colourways and an integrated rangefinder mounting plate - and we'd be building one of the very first new models to roll out of the factory.
Indeed, the exact 2025 Q Follow trolley you will watch being built in the video below is also being given away to one lucky entrant. You can find out how to enter the competition at the end of this article.
WATCH: Dan Parker builds his very own 2025 Q Follow trolley at Stewart Golf's HQ
Goods In & Quality Assurance

We started our day at the far end of the warehouse, otherwise known as Goods In. Here, as the name suggests, is where every part for every Stewart Golf trolley arrives before it is put through its paces by the quality assurance team, which will make sure each part. We were joined for the day by Stewart Golf CEO Mark Stewart, who talked us through the processes behind making an electric golf trolley at Stewart Golf.
"All of our parts are made by specialist subcontractors, mostly in the UK," Mark explained. "Everything comes through this door, and this is where we'll check for quality and make sure everything is doing what we want it to do and is made how we've designed it."
The engineers at Stewart diligently check all the parts that come into the factory before they hit the assembly line. A cutting-edge measuring machine is on hand to precisely measure and check even the most awkwardly shaped part of a Q Follow trolley down to the millimetre.
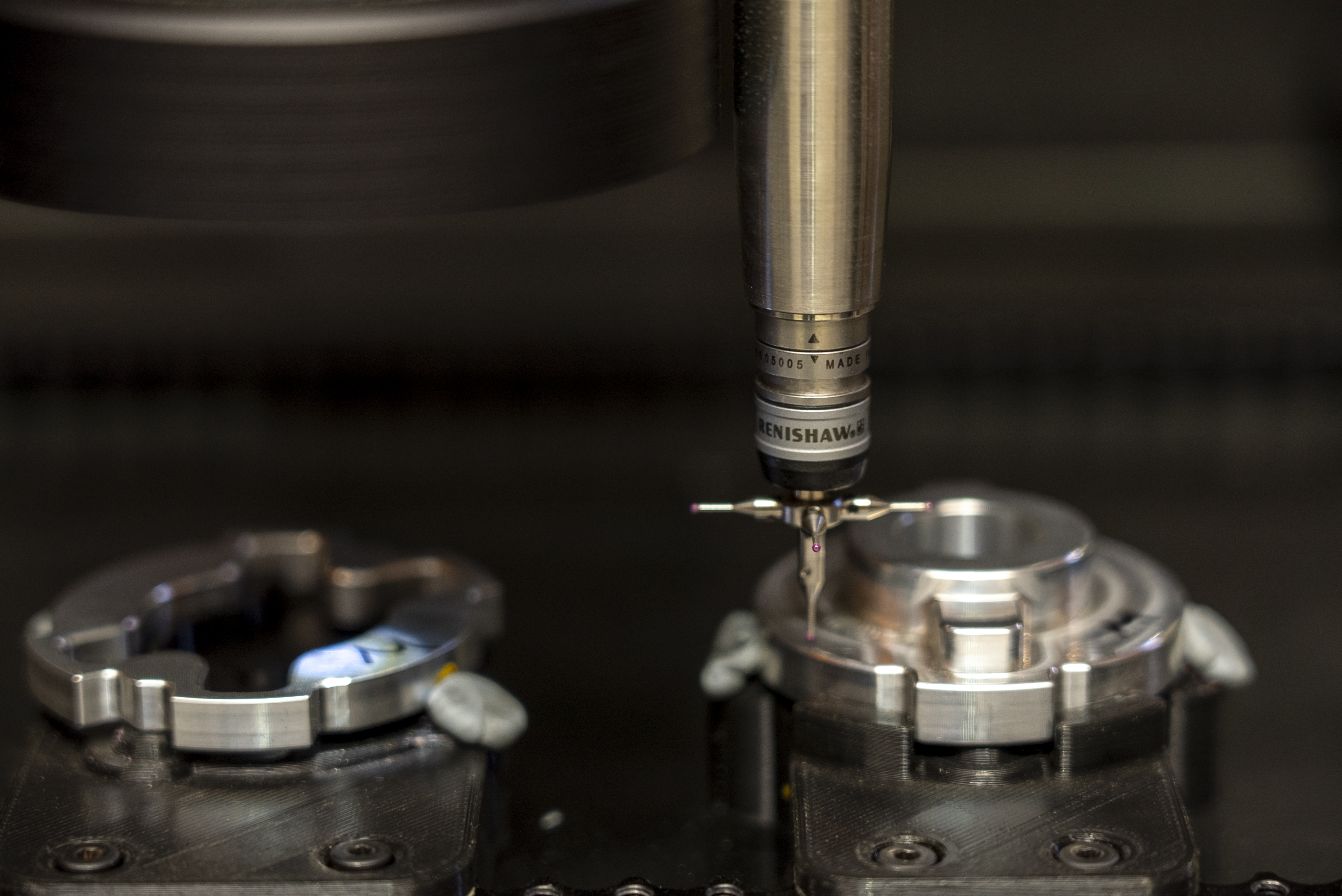
"It could be anything, so even the wheels of the trolleys. How do we know for sure that the wheel is round? How do we know that all of the other parts that attach to the wheel fit into it easily? What we want to do by the time we get to the production line is know that what we're putting together is of high quality. You can't test quality into a product, you have to build it in."
"Effectively, we're an engineering company that happens to be in the golf industry. First and foremost, we have to engineer our trolley properly. If we engineer it properly, then the product will be good, and if the product is good, the experience for the customer is good too."
Design Philosophy & Prototyping
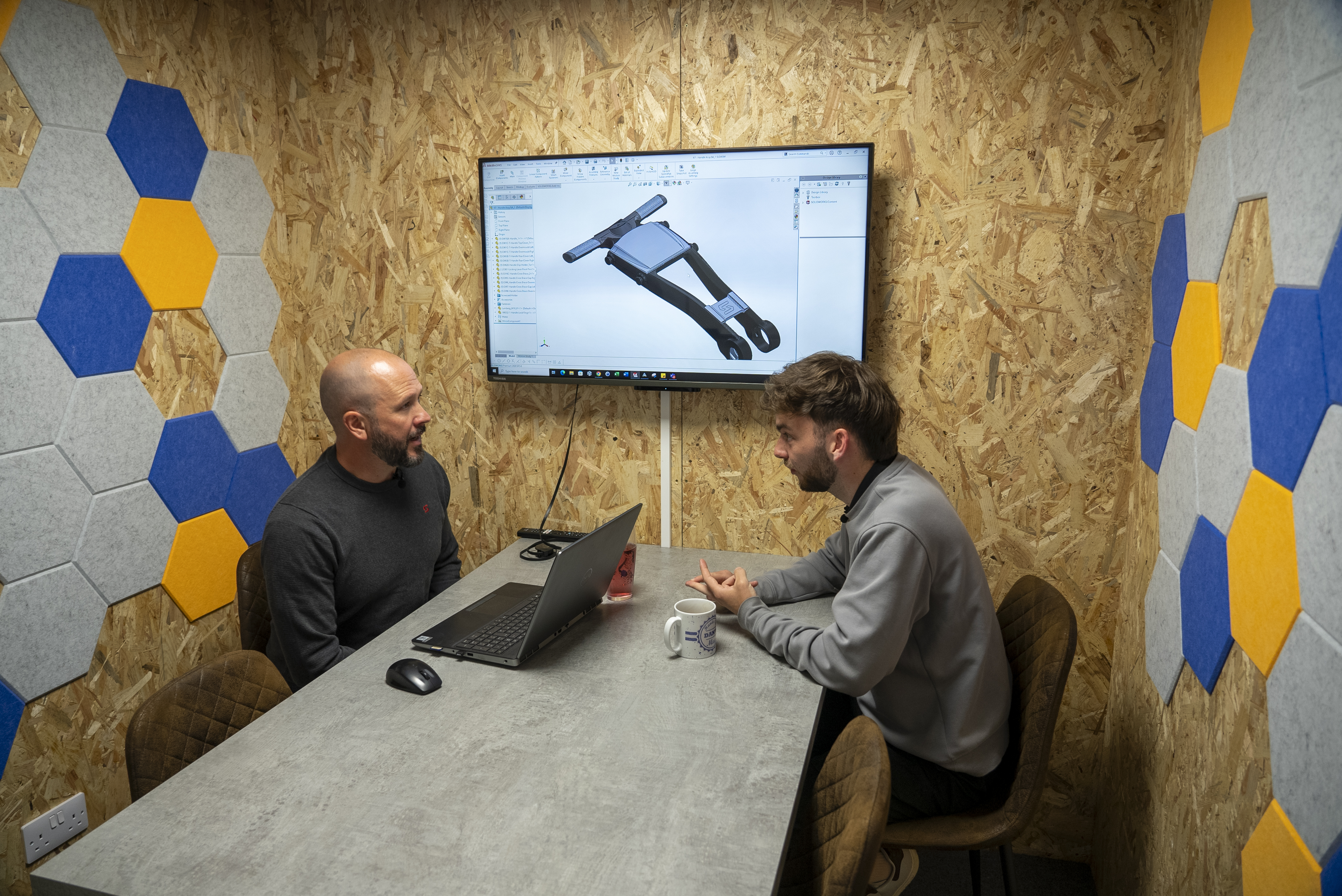
Before anything can arrive to be quality checked on the goods in part of the factory, it has to be ideated, designed and prototyped before heading into mass production. Mark gave us a sneak peek into Stewart's design philosophy and prototyping process for its award-winning range trolleys.
"The four of us who started the business are all still here. We're all engineers, so coming up with things, innovating and designing is what we do - it's in our DNA. So when we come to design products, we're looking at how we're going to give the consumer the best experience on the golf course."
"For the first ten years, we were remote control trolley specialists, because that's all we designed at the time, and when you design something with these specificities, you have different priorities that you would for any other type of trolley, namely balance."
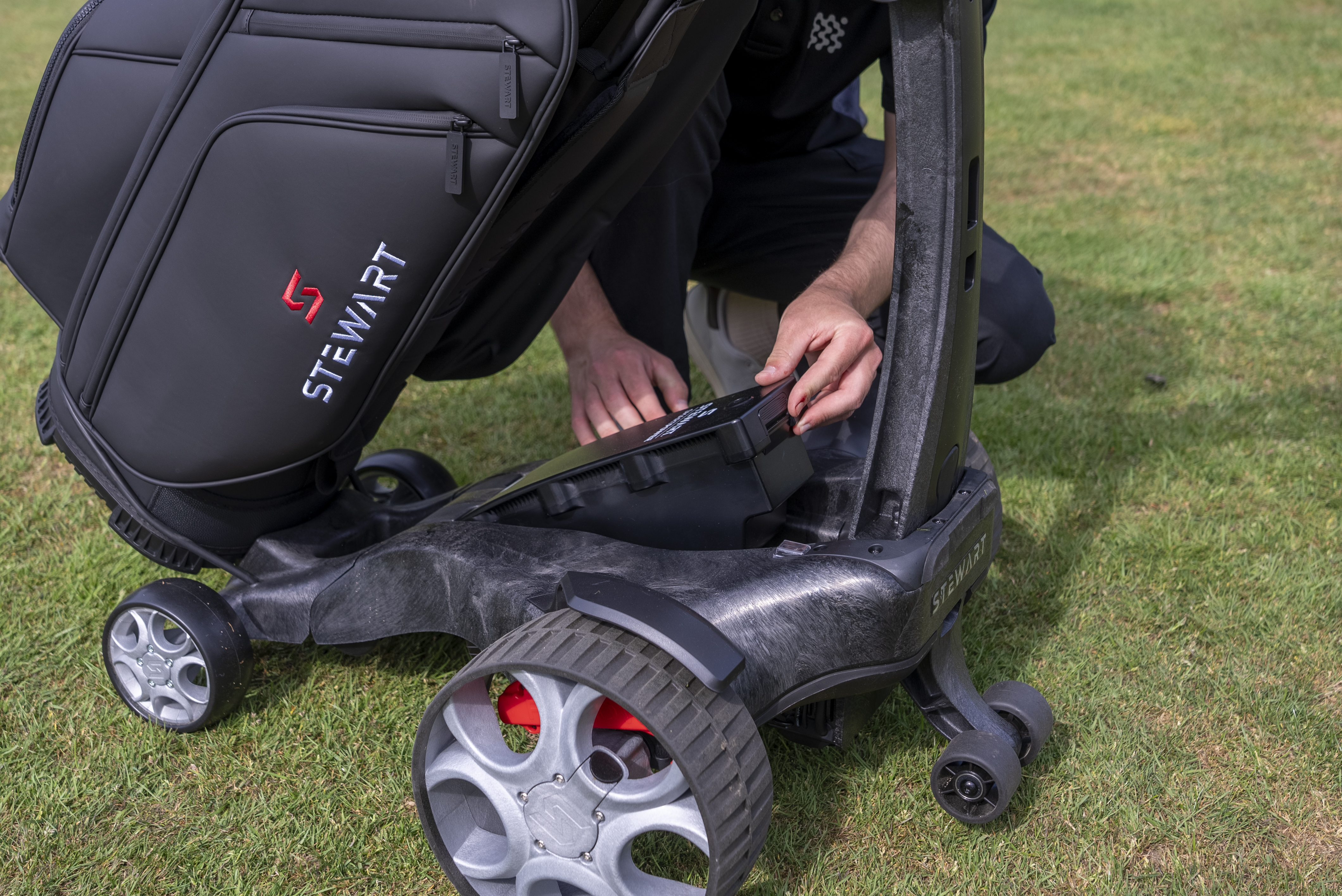
"When designing a remote control trolley, we're designing a product that is likely going to be 20, 30, 40 yards or more ahead of a person, so we need to design a product that gives golfers the confidence it's not going to fall over ahead of them. Our priorities have always been on stability, which is why we design with a wider wheel base, use two front wheels instead of one, utilise a stabiliser at the back, and move the battery further forward in the chassis."
The theory behind the way Stewart designs its Remote and Follow trolleys is all about balance and instilling confidence in the user that the trolley will be able to stay upright across any terrain, but how do these designs make their way to the factory to be built?
"We use Solid Works, which is an industry-standard software for designing components for our products. We have to go into extreme detail on this stuff because it's expensive to get started. Something like the Q Follow has years of design and prototyping that go behind it, and by the time you get to a stage where we know exactly what we're going to make and how we're going to make it, we're in for hundreds of thousands of pounds of commitment. We'll do all of this in-house, too, so we have control over the whole process."
Assembly & Final Checks
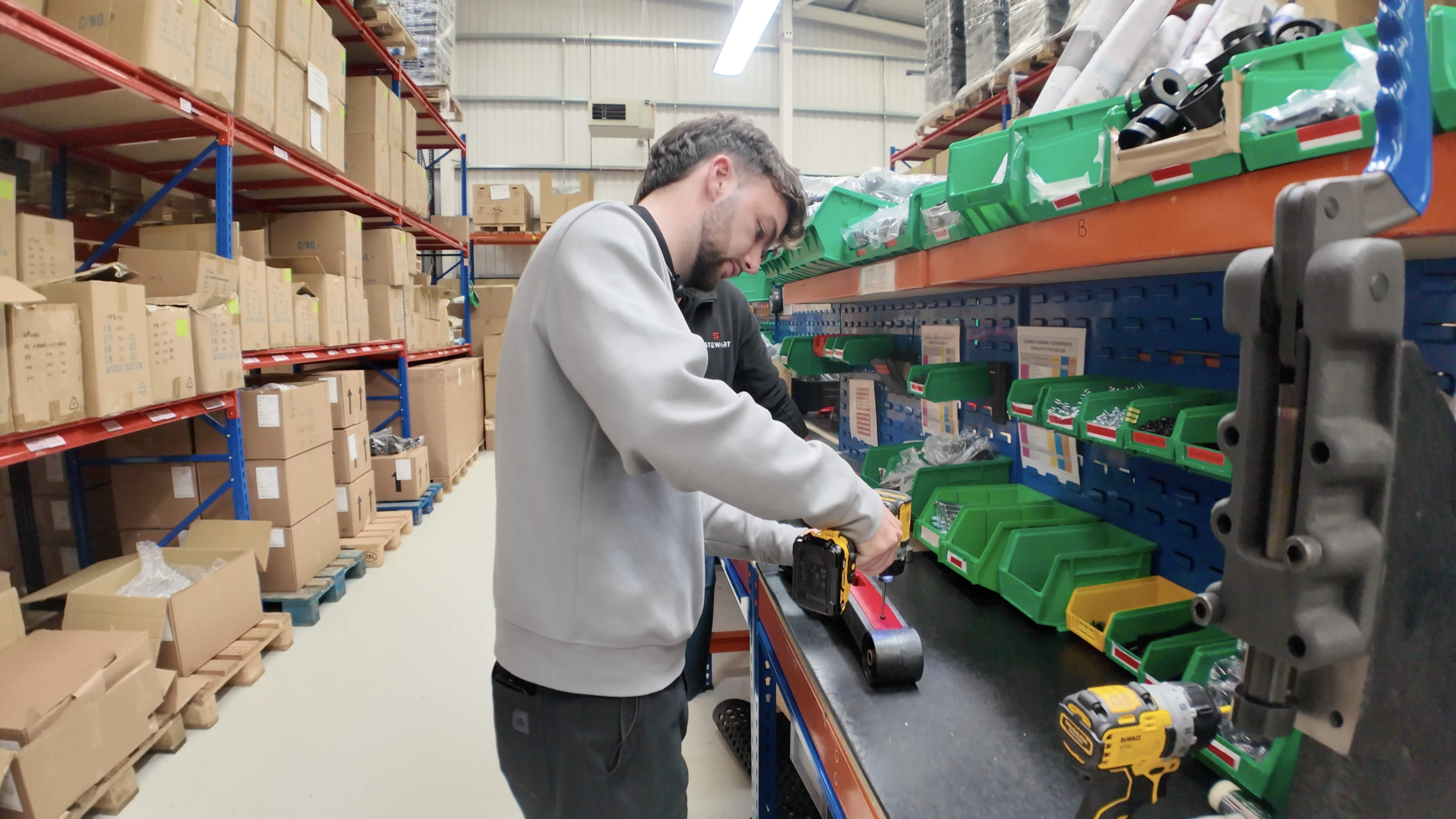
Now with a much better understanding of how the parts of the Q Follow came to be on the assembly line, it was time to try our hand at putting it together. We met Ash, Stewart Golf's Production Manager, to guide us through the process and learn just how the Q Follow comes to life in its very final stages of production.
"Typically, we've got either three or six members of staff working on the production line, depending on how many trolleys we want to produce on that day. Three members of staff can produce 24 units in a day, and six staff can produce 48 units per day. From start to finish, it's normally about 60 minutes."
As you can see in the video, most of the heavy work has been done in the design and quality check process. It makes the physical assembly of the Q Follow as straightforward as piecing it together with screws and giving it plenty of TLC.
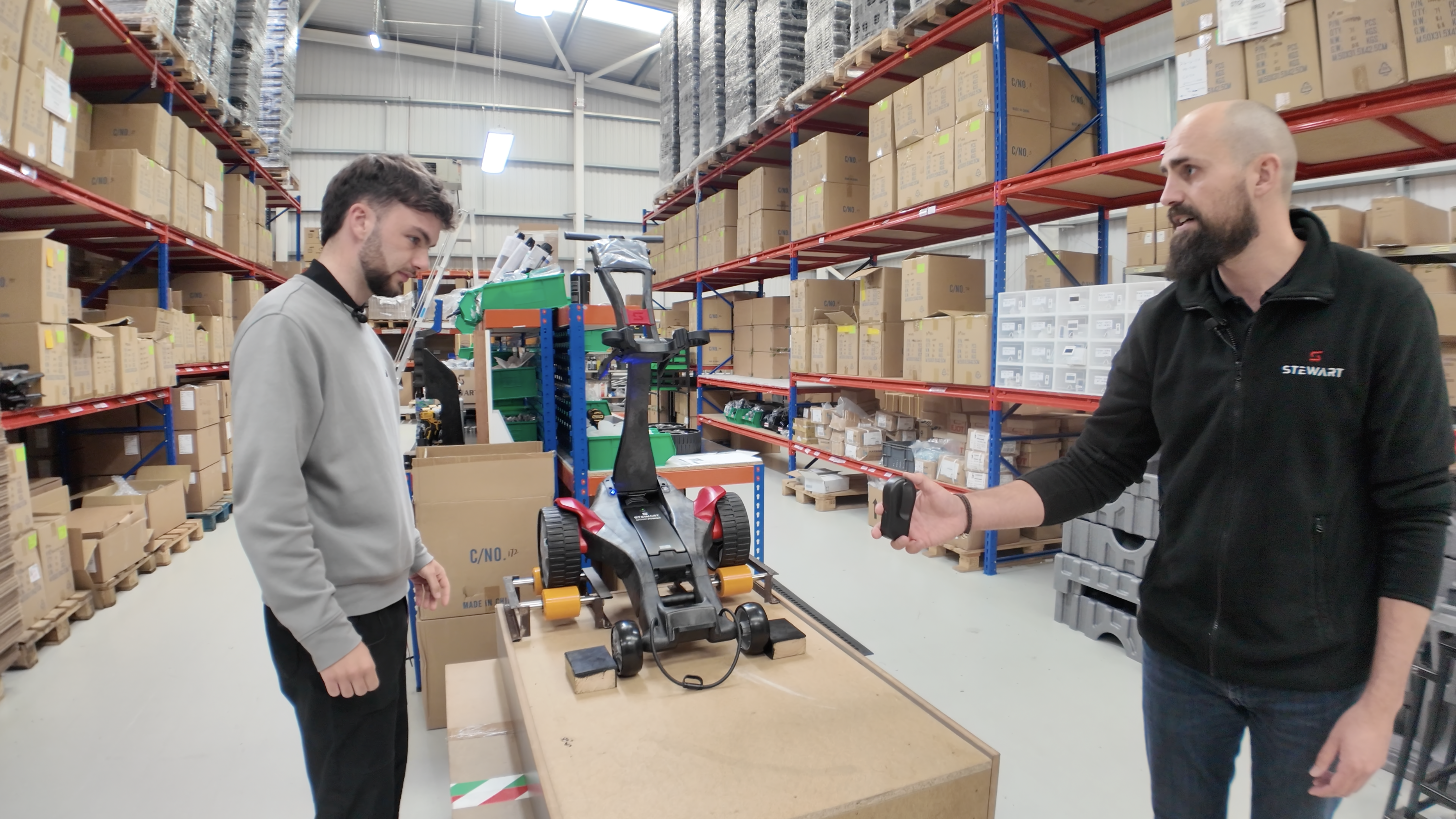
The 2025 Q Follow is now available with customisable coloured panels for the first time, something that Stewart's design process allows them to achieve with relative simplicity for them and the consumer. Golfers can now also choose between grey and black wheels, while the inclusion of a new integrated rangefinder mounting plate is another addition to the 2025 update of the Q Follow.
"We're adding these customisation features simply because we can. We build and design everything in-house, and we wanted to offer a level of customisation to the product that others simply can't offer."
Before the Q Follow is ready to leave the factory, the last part of the assembly process is a thorough test. The unit is placed on a rolling road, where the remote and follow functions can be tested thoroughly to make sure everything is working as it should. The final, final touch is then applying the Stewart decals to the back of the chassis, ready to be boxed up and sent away. Of course, the trolley that we made in this video isn't being boxed up to be sent away; that's because it's being given away to a lucky winner of the competition.
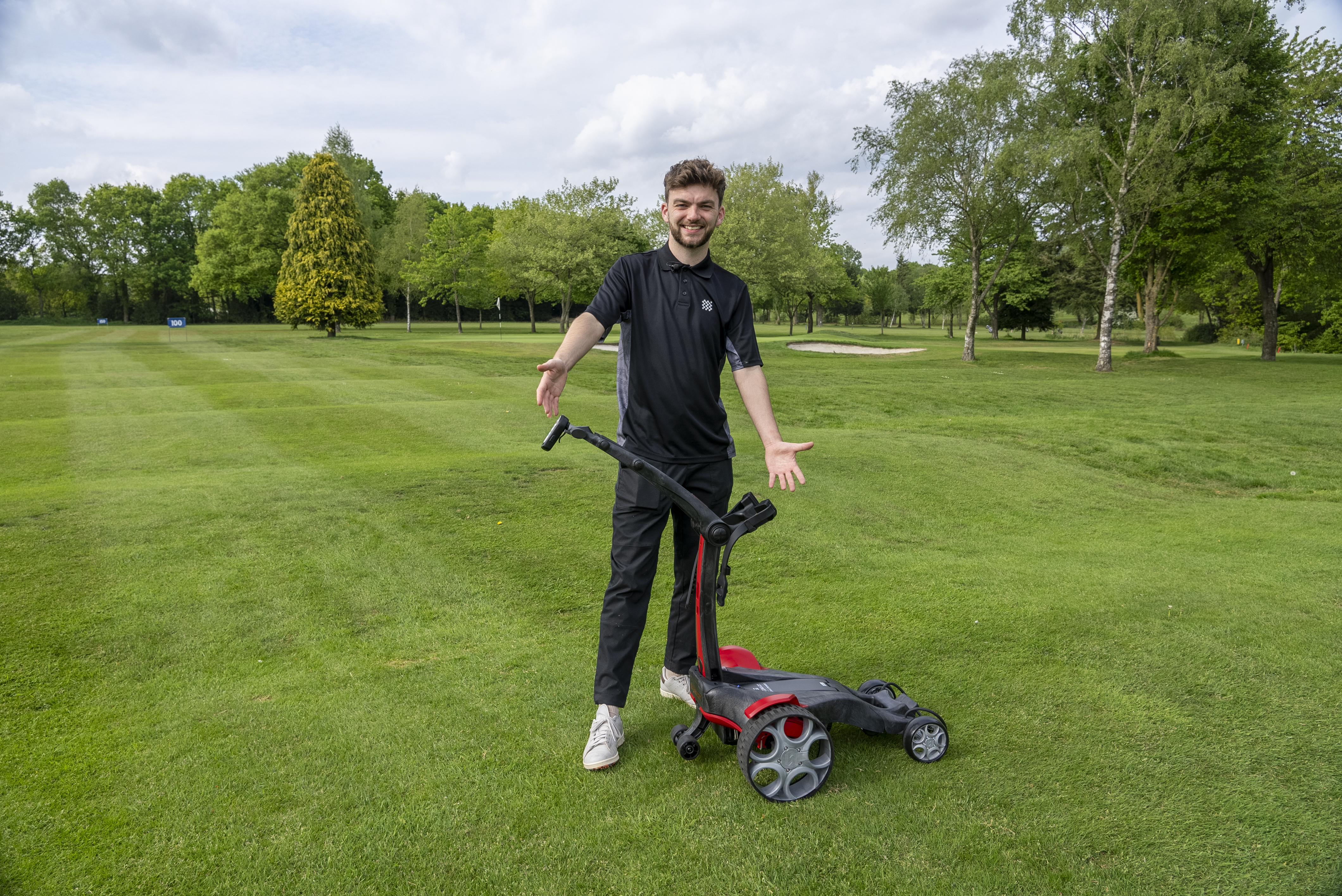
We took our trolley straight from the factory onto the golf course to check our handiwork. After a few holes of testing the Remote and Follow functionality and making sure all of the folding mechanisms worked, we were happy our Q Follow was ready to go.
To enter this fantastic chance to win the exact 2025 Q Follow trolley you've just watched being built, visit the Stewart Golf website and follow the instructions on the form - good luck!