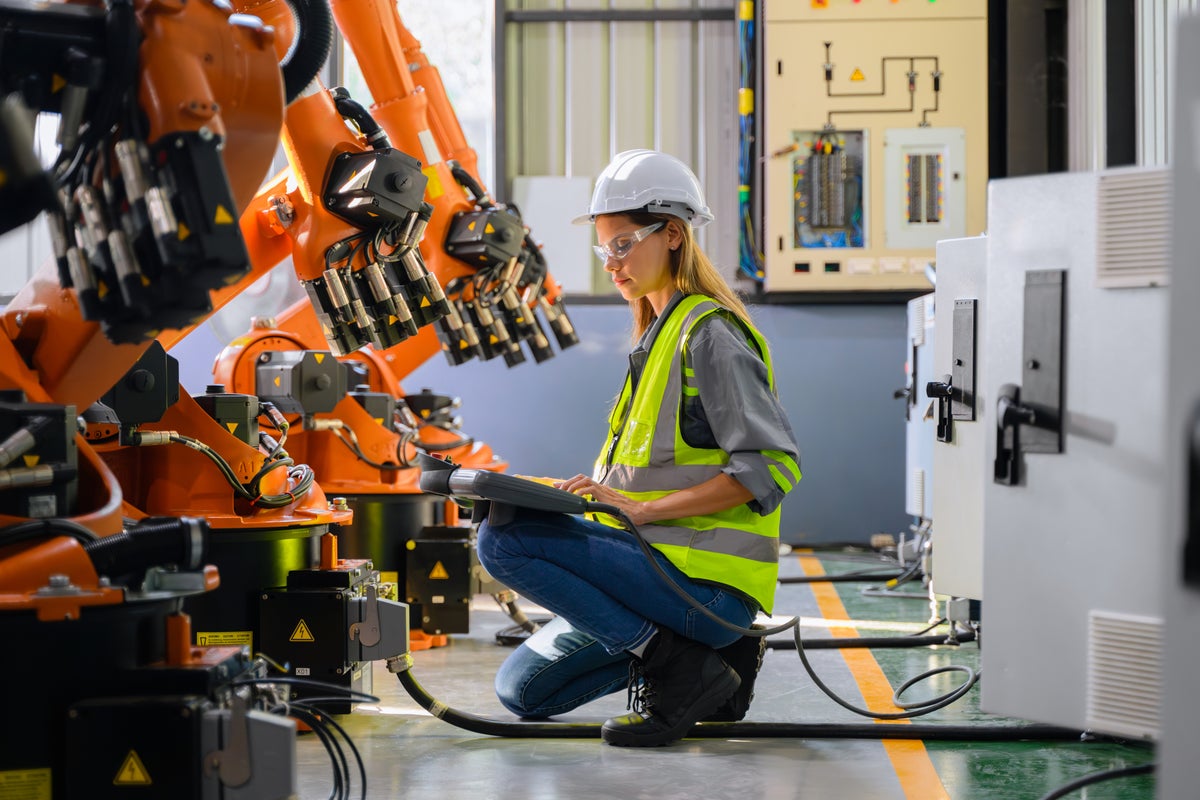
Phoenix Contact is a Business Reporter client.
With more and more organisations undergoing digital transformation, it’s helpful to understand how data and analytics drive change and help build sustainable enterprises
Picture this – a robot strolls up to your machines, inquires about their performance, predicts potential hiccups, and offers quick intervention to enable maximised efficiency.
While we may not be there yet, thanks to the power of real-time data, the vision is closer than ever. We are already on track to transition to a world where machines communicate with each other to share their needs and potential issues, leading to improved efficiency, enhanced collaboration, reduced downtime and improved energy consumption.
We are living through the fourth industrial revolution, aka Industry 4.0, characterised by increased automation and integration of smart machines.
Growing at a CAGR of 20.67 per cent, Industry 4.0 is the next phase of digital transformation driven by disruptive trends such as IoT, cloud, machine learning, data and analytics, human-machine interaction, robotics and advanced manufacturing technology.
We are generating troves of data
In 2016, Cisco Systems shared a blog post highlighting that the world’s collective internet usage had crossed the “zettabyte threshold”, having generated 1024 trillion terabytes and thus officially entering the “Zettabyte Era”.
It took all of human history until 2016 to create one zettabyte. However, in 2022 alone, global IP traffic was at 333 exabytes (equivalent to a third of a zettabyte).
While we may be generating an astonishing amount of data, it’s of no use until we learn to strategically use it. While data can be a powerful resource, in today’s information-drenched world, the value of data lies not in its volume but in how it’s harnessed.
How we use data to get meaningful insights and drive actionable outcomes makes all the difference.
Manufacturers are moving towards data-driven sustainability
Data-driven sustainability means collecting and using data to make decisions that not only lower greenhouse gas emissions but also optimise supply chains, reduce waste, and power a positive change while increasing profitability.
With a focus on long-term value creation, business leaders are turning to data-driven solutions to build resilient, purpose-led organizations that prioritise the environment alongside business goals.
Embracing sustainability is no longer optional
Climate change is a very real threat, driving many organisations to look for ways to operate more sustainably. According to the Global Lighthouse Network Fourth Industrial Executive Survey, nearly 77 per cent of respondents see productivity, sustainability or resilience as their top priority.
Manufacturers are building smart factories equipped with advanced sensors, embedded software and robotics that collect and analyse large amounts of data. This ensures real-time visibility of manufacturing assets. This data from production can be combined with operational data from ERP, supply chain, customer service and other enterprise systems to create even higher value with whole new levels of visibility and insights from previously siloed information.
Real-time data enables various opportunities for sustainability, including:
- Improving efficiency in energy consumption for a reduced carbon footprint
- Predictive maintenance for reduced equipment downtime and resource consumption
- Enhanced collaboration to foster a culture of effective, data-driven decision-making
- Real-time monitoring for quick and effective intervention to prevent costly disruptions
- Increased automation for maximised efficiency, precise resource allocation and minimised human error
This data-driven decision-making leads to improved process optimisation and a new level of efficiency not previously possible, helping companies achieve carbon neutrality.
Preparing your business for Industry 4.0
“On paper, Industry 4.0 and digitalisation make a ton of sense, but if your organisation isn’t properly prepared, your manufacturing team could be in for a rough transition. Digital transformation is not just about technology. It’s a holistic approach that reshapes business processes, culture and customer experiences,” says Zachary Stank, Product Marketing Manager – Automation Systems and Safety, Phoenix Contact USA.
We are witnessing an unprecedented global paradigm shift. Digitalisation, networking and globalisation mean there are new market requirements. Classic system structures are developing into globally interlinked production systems.
The pace of innovation means technologies are converging rapidly, and products and infrastructures are becoming more intelligent. Young engineers and software specialists are shaping new working methodologies, and cloud and edge computing are making future-oriented, industrial business models possible.
Many companies are looking at rethinking and changing processes. This makes flexibility a pressing requirement because an adaptable, fully networked manufacturing setup can respond quickly to new requirements and volatile markets.
Traditional PLCs have been the backbone of industrial automation for decades, but as the industry shifts towards a more IIoT-forward landscape, their limitations become more glaring. And proprietary development ecosystems, lack of support for modern communication protocols (such as MQTT or OPC UA) and outdated cyber-security measures make digital transformation difficult.
PLCnext Technology from Phoenix Contact provides a powerful solution to embed data-driven decision-making in your applications while offering a flexible solution with open architecture. It builds a bridge between the OT and IT levels and, in addition to efficient data collection, enables smooth data exchange between all systems and devices. This is made possible by standardising the data so it is available transparently on all levels and can be used in the production process in a useful way.
As an open ecosystem for industrial automation that consists of open hardware, modular engineering software, a global community and a digital software marketplace, PLCnext Technology helps organisations benefit from new forms of collaboration.
PLCnext Technology extends the use of familiar PLCs in ways that will change the future of industrial automation.
Learn more about how Phoenix Contact USA can help manufacturers make data-driven decisions to enable sustainable manufacturing.