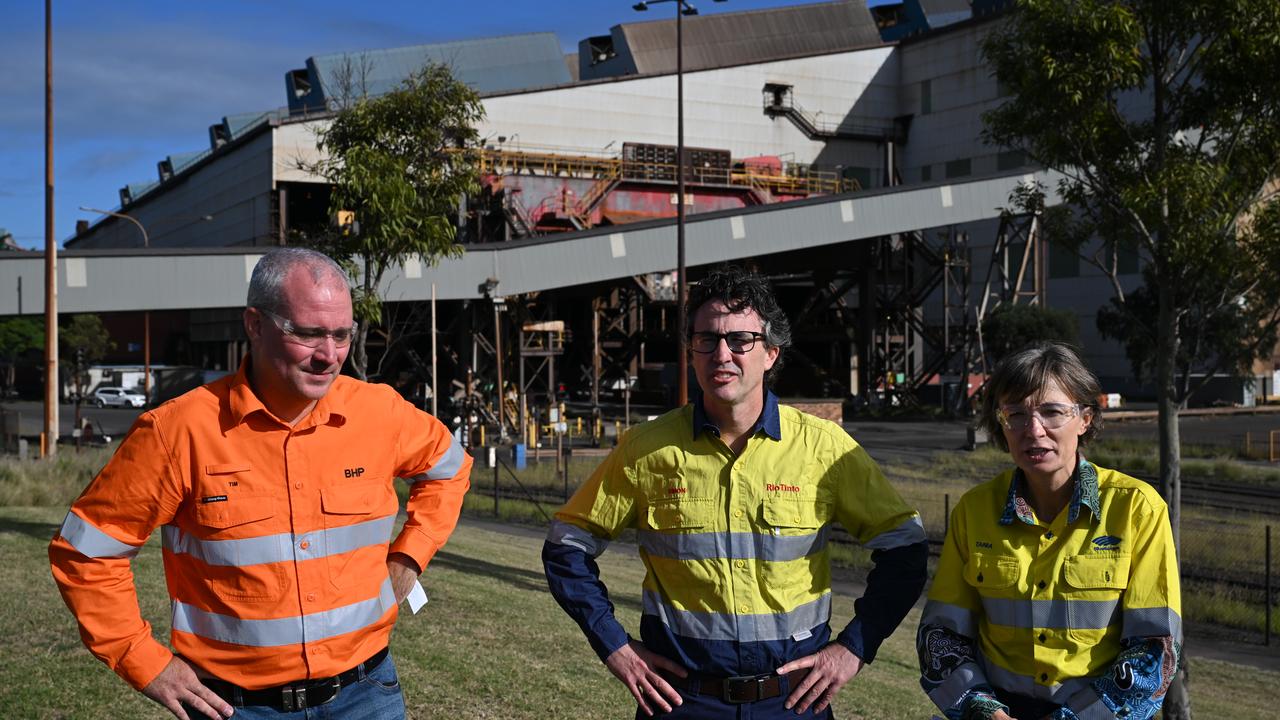
Two of the world's biggest iron ore producers and Australia's biggest steelmaker are joining forces to slash the carbon footprint of steel with a new type of furnace.
BHP, Rio Tinto and BlueScope pledged on Friday to work together on the country's first iron-making electric smelting furnace (ESF) pilot plant.
The agreement, announced at the Port Kembla steelworks in NSW, will draw on the mining giants' iron ore from Western Australia's Pilbara region and BlueScope's technical experience in manufacturing.
The project aims to demonstrate that the production of molten iron from Pilbara ores is possible when using renewable energy combined with direct reduced iron (DRI) process technology.
The move has the potential for wider adaptation across the global steel industry, which is one of the biggest sources of greenhouse gas emissions.
Rio Tinto iron ore chief executive Simon Trott said better ways must be found to enable the vital material for construction and engineering to be made more sustainably.
"The carbon intensity of iron and steelmaking requires profound change to meet the needs of our planet and our climate objectives," he said
The collaboration follows more than two years of work by Rio and BlueScope on the "electric melter" technology.
The partners will assess several locations in Australia for the proposed pilot plant that will need supporting infrastructure, a ready workforce, and access to industry and supply chain partners.
BHP's incoming WA iron ore president Tim Day said it was a "potential breakthrough" in reducing carbon emissions from steel production.
"Combining our expertise, we hope to help fast track near-zero emission-intensity pathways for steelmakers using Pilbara ores," he said.
"Technology pathways compatible with renewable energy and scalable to the order of hundreds of millions of tonnes of steel production would be a major step forward in setting up Pilbara ores, and the world, for a low greenhouse gas emission future."
A pre-feasibility study is expected to be completed at year-end and, if approved, the pilot plant could be commissioned as early as 2027.
The tie-up will be "key to cracking the code for Pilbara ores in low emission-intensity iron-making", according to BlueScope's chief executive for Australia Tania Archibald.
"We believe DRI is the most prospective technology to decarbonise our Australian business, and the development of ESF technology is key to unlocking Australia's unique advantages," she said.
Together, the DRI-ESF equipment can replace the blast furnace, eliminating the need for metallurgical coal and potentially resulting in 80 per cent fewer emissions than conventional blast furnace steel.
Other options such as electric arc furnaces require high grade iron ores or scrap steel.
The proposed plant allows for greater flexibility in input raw materials, addressing one of the key barriers to wider adoption of low carbon emissions technology, according to the partners.
The method could also be integrated into a steel plant's existing downstream production units.