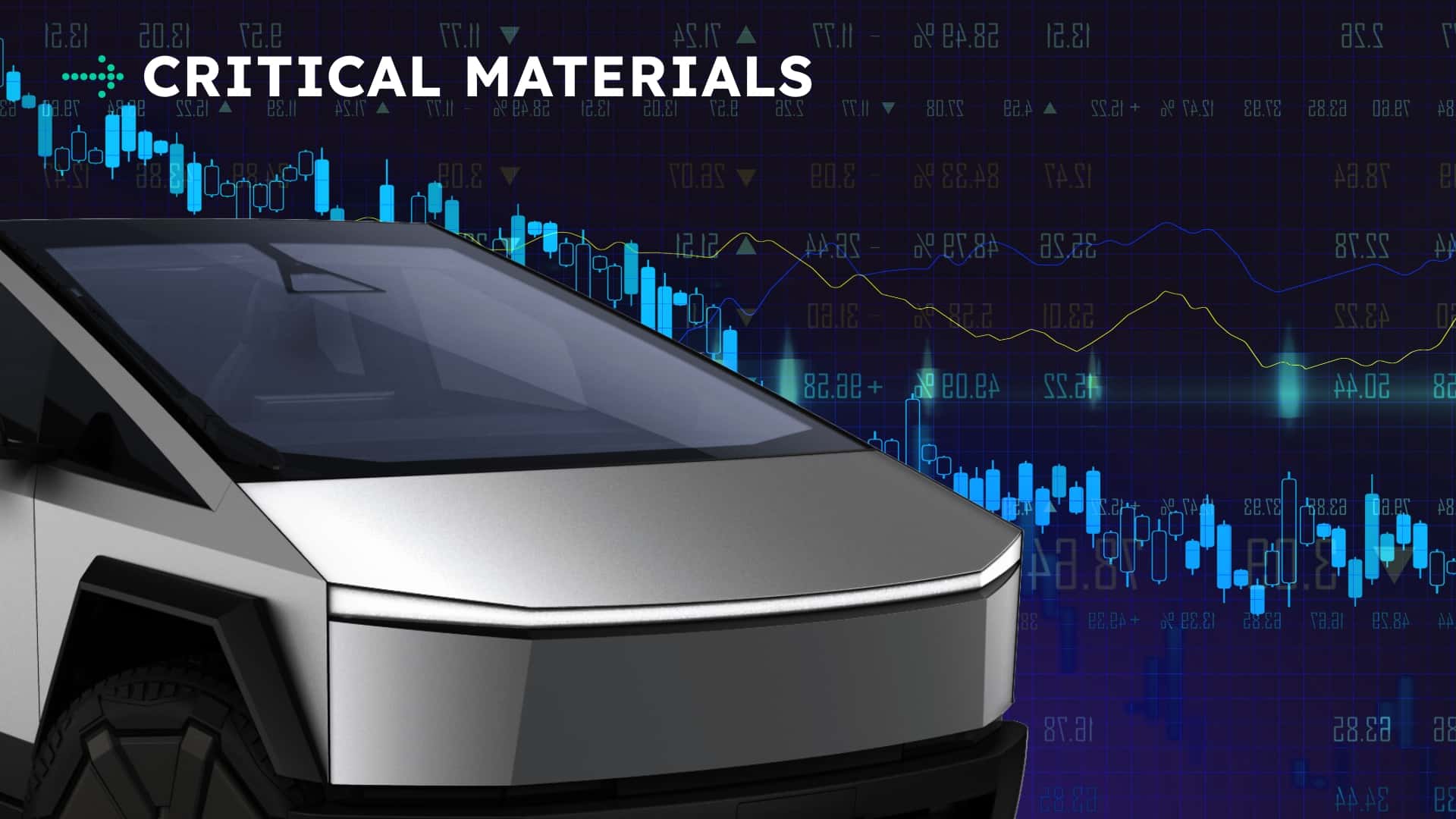
Tesla's futuristic Cybertruck was something that CEO Elon Musk once admitted could flop. However, that thought seemed to be unlikely—the truck was basically a rolling billboard, essentially a modern-day DeLorean. And much like the DeLorean, the truck seems to be facing a demand issue that's causing units to pile up almost as quickly as Tesla can produce them.
Welcome back to Critical Materials, your daily roundup for all things electric and tech in the automotive space. Today, the Tesla Cybertruck inventory has reached critical mass, Hyundai's hypercasting plant gets kicked down the road, and Rivian greenlights a new supplier plant. Let's jump in.
30%: Tesla Cybertruck Inventory Stockpile Balloons To More Than A Quarter's Worth Of Trucks

After reaching nearly two million estimated preorders, the Tesla Cybertruck was expected to shatter sales records. After all, there is nothing else like it on the road today, so folks who wanted something different and electric could easily pick up this pickup and check two boxes at once. Unfortunately, once the truck finally debuted, the only record it seems to be shattering is Tesla's parking capacity.
According to new data from the inventory tracking site Tesla-Info, Tesla is sitting on a record number of inventory units of its flagship Cybertruck. How many, you ask? Try a whopping 10,000 units, according to the data reported on by Electrek. This means that the automaker officially has more trucks lined up on lots like dystopian lawn ornaments than it managed to sell through the first three months of this year.
Let's back up for a second and talk about that.
Demand for the Cybertruck (like most Tesla products) has been crashing over the last few months. The automaker managed to produce an estimated 6,400 units of its stainless steel pickup during the first quarter of 2025, according to data from Cox we reported on last month. That represents just 21% of Giga Texas' Cybertruck capacity. But more importantly, it's 3,600 units less than the total number of trucks Tesla is reportedly sitting on right now.
This wasn't supposed to happen. Back in 2019 when Tesla revealed the Cybertruck and tested its war-grade glass by chucking a giant metal ball at the window, the world was told that the future was trapezoidal. And they all believed it. Buyers lined up to put $100 down to save their place in line, giving Tesla a free loan while the automaker spent the next four years readying deliveries. During that time, the truck's price skyrocketed and the range Musk promised never came to be. And then he began his transformation into a pseudo-politician.
Suddenly, it became uncool to own a Tesla.
If you couldn't tell, Tesla's brand image is in the toilet right now. The automaker blamed that on "changing political sentiment" in its quarterly earnings report, noting that its sales could be affected in some markets. In reality, people are lashing out (seemingly against Musk's recent political activism) and treating Cybertrucks like blank canvases for vandalism.
Tesla has since exhausted its reservation list and it still needs a way to sell the trucks. Despite piling cash on the frunk and even releasing a cheaper model, the cache of Cybertrucks continues to climb. By the looks of it, Tesla may have an issue selling even 10% of the 250,000 annual units it initially planned to sell.
60%: Hyundai Delays Hypercasting Plant To Focus On U.S. Production

Hyundai's big, hot, molten-metal dream of using gigacasting tech in its future cars has been put on ice. According to The Korean Car Blog, the automaker has decided to stall the plans for its first "hypercasting" plant—that's what Hyundai is calling its own version of gigacasting—until 2028.
The project was originally slated to take place at Hyundai's massive production facility in Ulsan, South Korea. This plant houses five different manufacturing plants for Hyundai, plus facilities that build its engines and transmissions. Hyundai says that it's the "world's single largest automobile plant," and adding hypercasting into the mix would allow it to significantly cut costs. So why stop now?
According to Hyundai, the rippling effects of U.S. auto tariffs are at least partially to blame. Here are the specifics from The Korean Car Blog:
Hyundai Motor Company is reportedly postponing the launch of its cutting-edge hypercasting production facility at the Ulsan plant, a project originally backed by a [$730 million] investment. The decision comes in response to weakening global electric vehicle (EV) demand and the United States’ recent imposition of a 25% import tariff on foreign automobiles.
According to Seoul Economy in the automotive industry on May 10, Hyundai is in discussions to delay the mass production start of its hypercasting facility from 2026 to 2028. This adjustment is being negotiated with the labor union at the Ulsan plant, following talks that began late last year.
If you're not familiar with gigacasting tech, here's a brief explainer.
Cars have been made using a ton of stamped metal parts for decades. This requires manufacturers to fasten these stamped parts together to form a vehicle body. Rather than shape, cut and fasten, automakers have been looking for more efficient ways to build cars that reduce parts cost and labor. The answer? Gigacasting—or, in Hyundai's case, hypercasting.
Essentially, this is forcing molten metal into a large mold to form all of the parts that would otherwise need to be stamped out of sheet metal and then welded or riveted together. In Tesla's case, gigacasting allowed the company to eliminate 370 parts and more than 1,600 welds from the Model Y, all while reducing weight by 10% and improving overall vehicle efficiency.
Now, back to Hyundai.
The Korean automaker says that softening demand for EVs and the U.S. tariffs have really mucked up its profit projections. Combined, the two have created the perfect "demand chasm" in the EV market, especially since Hyundai exported more than 1 million of the 1.7 million vehicles it sold in the U.S. from South Korea. In fact, Hyundai projects that the cost to import each vehicle into the U.S. will increase by roughly $5,900—or a significant bottom-line hit of around $5.9 billion.
Rather than withdraw from the U.S. market, Hyundai is instead focusing on domesticating production in the States over the next four years. This has required an investment of around $9.3 billion into its Metaplant in Georgia to raise its annual production output to around 500,000 vehicles. Hyundai hopes to have a combined U.S. production output of around 1.2 million vehicles annually across all its facilities.
It's clear that Hyundai is looking for a way to better utilize its funds. Sure, hypercasting can save as much as 40% in some production costs, but do those savings cover the funds otherwise gobbled up by new tariffs? Hyundai clearly sees a better use of its funds in bolstering production in the U.S. to offset these costs before spending more on hypercasting. It's not eliminating that process completely, only kicking the can down the road a few years.
90%: Rivian Greenlights New $120 Million Supplier Park In Illinois

Rivian has officially greenlit building a new 1.2 million square foot supplier park right next door to its existing assembly plant in Normal, Illinois.
The automaker announced the plans for its $120 million investment on Monday alongside Illinois Governor JB Pritzker. Rivian will receive a $16 billion tax incentive to support growing the company and says that this new supplier park will help bring the upcoming Rivian R2 to life alongside its existing R1T, R1S, and commercial vans.
From the governor's press release:
As part of this, Rivian will invest nearly $120 million, which will enable the company to develop the supplier park and create nearly 100 new direct jobs. This significant investment will pave the way for EV suppliers to locate in the park and create hundreds of new jobs while bolstering the supply chain and manufacturing ecosystem in Illinois. Construction on the supplier park is underway and is expected to be completed in 2026.
The park will allow the company to co-locate suppliers that produce component parts for Rivian vehicles, with the parts transported across Highway 150 to the company's main facility for assembly into the final R1 and R2 Rivian models. Hosting key suppliers nearby will help Rivian fortify their supply chain, which increases consistency and continuity in the manufacturing process.
I know what you're wondering: what exactly is a supplier park?
Imagine some sort of industrial food court. But rather than picking up lunch from Cinnabon, Sbarro or Panda Express, you're shopping around for the components you need to build vehicles. Basically, it's a way to co-locate some of its key suppliers extremely close to its production facility without having to vertically integrate every single piece of the car puzzle.
Rivian says that this new facility will allow it to reduce shipping, logistics, and warehousing costs significantly. And with an underground tunnel bridging the two sites, Rivian is able to easily transport completed parts between the supplier park and its plant.
You might remember that Rivian is also building a giant factory in Georgia. Those plans haven't gone anywhere. The automaker says that it's still on track to begin production at that plant in 2028, but to get its Model-Y-fighting Rivian R2 on the road sooner, it plans to start production in Normal next year. This means also adding on a previously-announced 1.1 million square foot expansion onto its existing plant to prepare its facility for R2 and increase annual output capacity from 150,000 to 215,000 vehicles. For comparison, Rivian expects to deliver around 50,000 vehicles in 2025. Once Georgia goes online, Rivian should have the capacity to produce around 400,000 EVs each year.
100%: Are The U.S. Tariffs Stifling Innovation?

News that Hyundai is stalling its plans to set up a new hypercasting shop is a bit concerning. It's not that the automaker can't do it, just that it has to re-prioritize its spending in order to stay afloat while the U.S. tariffs wreak havoc on the brand because it imports most of the vehicles it sells stateside.
Automakers now have all kinds of problems to figure out. Not only do supply chains have to be reconfigured to meet the new normal, costs must be reeled in to help absorb some of the tariff impact. Of course, the added costs could simply be tacked on to the vehicle's sticker price, but that will lead to a hit on sales. Beyond all that, there will almost certainly be a trickle effect that dips into new vehicle development and tech innovation, too.
All that being said, do you believe that the new tariffs on vehicles and parts imported into the U.S. are stifling innovation? And if so, just for the U.S., or globally? Let me know your thoughts in the comments.